Indian Auto Component Industry To Grow By Upto 10% In FY2026 Says ICRA
- By MT Bureau
- February 20, 2025
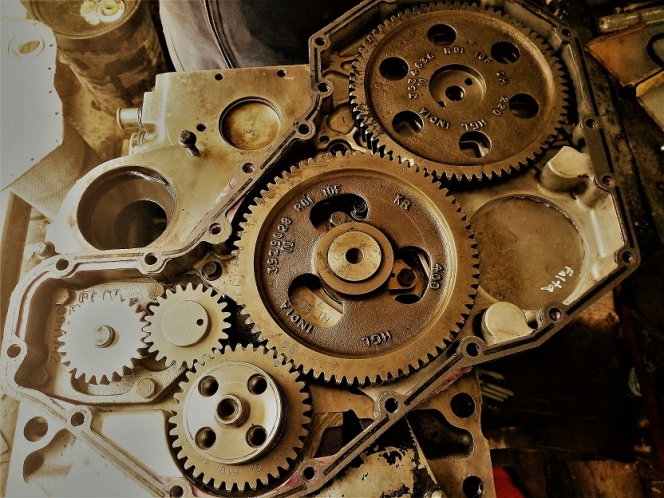
The Indian automotive components industry, which is a critical partner for the domestic as well as the global automotive industry is expected to grow by 8-10 percent in FY2026 according to ICRA.
The estimates are based on the company’s assessment of about 46 auto ancillaries with aggregate annual revenue of over INR 3,000 billion in FY2024, which accounted for about 50 percent of the industry.
For FY2025, the industry is expected to report 7-9 percent growth, with operating margines to be around 11-12 percent for FY2025 and FY2026. The confidence comes on the back of the industry benefitting from operating leverage, higher content per vehicle and value addition while remaining vulnerable to any significant unfavourable movements in commodity prices and foreign exchange rates.
The study stated that the ‘disruption along the Red Sea route has resulted in a surge in ocean freight rates by 2-3 times in CY2024 compared to CY2023. Any further sharp and sustained increase in ocean freight rates could also have a bearing on margins for auto component suppliers having significant exports/imports.’
In FY2026, ICRA estimates that the auto component sector will pump in INR 250-350 billion investment towards enhancing capacity, localisation/capability development and new technologies (including EVs) among others.
The big opportunity in EV segment can be seen on the fact that at present only 30-40 percent of the supply chain in India is localised, which includes traction motors, control units and BMS. On the other hand, EV battery cells that make up for almost 30-40 percent of an EV cost continues to be imported.
Vinutaa S, Vice President and Sector Head – Corporate Ratings, ICRA, said: "The domestic auto component industry is in a transitory phase with the automotive players increasingly focusing on sustainability, innovation and global competitiveness. Demand from domestic original equipment manufacturers (OEMs), which constitutes over half of the industry revenues, is estimated to grow by 7-9 percent in FY2025 and 8-10 percent in FY2026. Part of the growth would stem from premiumisation of components and higher value addition. Growth in replacement demand is pegged at 5-7 percent in FY2025 and 7-9 percent in FY2026, driven by increase in vehicle parc, higher average age of vehicles/used car purchases, preventive maintenance and growth in organised spare parts, among other reasons.”
“Exports, which account for close to 30 percent of the industry’s revenues, are likely to be impacted by subdued vehicle registration growth in the target markets. However, factors like rising supplies to new platforms because of vendor diversification initiatives by global OEMs/Tier-Is and higher value addition, partly stemming from increase in outsourcing, augur well for Indian auto component suppliers.”
Metal Castings & Forgings
ICRA finds that Indian component suppliers in the metal castings and forgings also have a bigger opportunity on the back of plants closure in European Union on the back of viability issues.
The report stated that ‘ageing of vehicles and sale of more used vehicles in global markets would aid in exports for the replacement segment. The impact of any import tariffs on Indian auto component exports remains monitorable.’
In the medium-to-long term, premiumisation, localisation, EVs and stringent regulatory norms continue to offer tailwind for the Indian automotive industry.
“ICRA’s interaction with large auto component suppliers indicates that the industry is estimated to spend INR 150-200 billion in FY2025 and another INR 250-300 billion in FY2026. The incremental investments would be made towards new products, product development for committed platforms and development of advanced technology and EV components, apart from capex for capacity enhancements and upcoming regulatory changes. R&D, though, is still at an average of 1-3 percent of operating income, significantly lower than the global counterparts. ICRA expects auto ancillaries’ capex to hover around 7-8 percent of operating income over the medium term, with the PLI scheme also contributing to incremental capex towards advanced technology and EV components,” he concluded.
Representational Image courtesy: Ronaldo Galeano/Pexels
- Tata AutoComp Systems
- Artifex Interior Systems
- IAC Group Slovakia
- Arvind Goel
- Manoj Kolhatkar
- Alan Fennelly
Tata AutoComp To Acquire IAC Group Slovakia
- By MT Bureau
- August 07, 2025
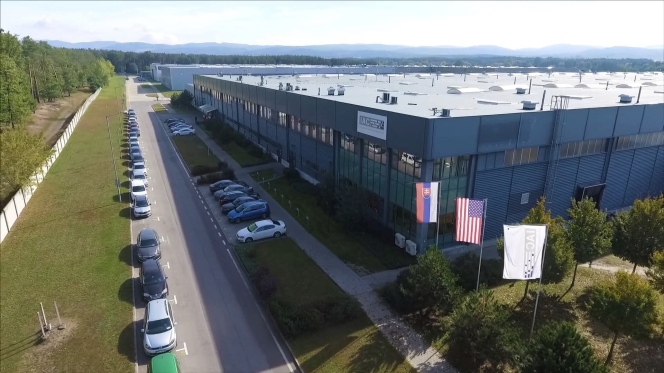
Tier 1 automotive supplier Tata AutoComp Systems, through its British subsidiary Artifex Interior Systems (Artifex), has signed a conditional agreement to acquire 100 percent stake in IAC Group (Slovakia).
The move is part of Tata AutoComp’s strategy to further strengthen its capabilities and expand its presence in the UK and EU markets.
Arvind Goel, Vice-Chairman, Tata AutoComp, said, “The acquisition of IAC Slovakia will mark a significant milestone in Tata AutoComp’s global growth journey. Following our earlier acquisition of Artifex, this step strengthens our European presence and reflects our commitment to serving global OEMs more effectively. IAC Slovakia’s strong operational excellence, skilled workforce, and strategic location will enhance our ability to deliver high-quality interior systems. This move supports our vision to be a trusted and value-driven partner in the global automotive supplychain.”
Manoj Kolhatkar, MD & CEO, Tata AutoComp, said, “We see strong synergy between IAC Slovakia’s capabilities and our existing European operations, which will enable faster integration and value delivery to OEM customers.”
Alan Fennelly, Chief Executive Officer, Artifex, said, “We are excited to welcome IAC Slovakia into the Artifex family. This expansion is a pivotal step in our journey to become the valued partner of choice. It strengthens our expertise in automotive interior systems, expands our capabilities, and opens the door to new partnerships and broader markets. I’m excited about what we’ll achieve together.”
Uno Minda’s Bet On Diversification Helps Net Profit Grow 46% In Q1 FY2026
- By MT Bureau
- August 06, 2025
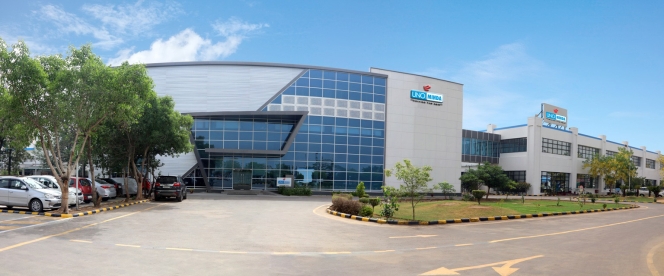
Tier 1 supplier Uno Minda has reported a robust INR 44.89 billion in revenue in Q1 FY2026, up 18 percent YoY, as compared to INR 38.18 billion last year.
The EBITDA came at INR 5.43 billion with a margin of 12.1 percent, as against INR 4.08 billion and a margin of 10.7 percent for the same period last year. The net profit grew by 46 percent at INR 2.91 billion.
Ravi Mehra, Managing Director, Uno Minda Group, said, “The automotive industry is undergoing a seismic transformation – driven by electrification, digitalisation, safety and premiumisation. At Uno Minda, we have embraced this change with agility and vision, positioning ourselves as a key enabler of next-generation mobility solutions. Our performance in Q1 FY26 reflects not only strong execution but also the growing relevance of our innovation-led portfolio across emerging technologies. We continue to invest in future-ready capacities, strategic partnerships, and R&D capabilities across India and overseas to deepen our technology leadership and enhance our value proposition to customers. We are confident that our continued emphasis on technology, quality, and customer-centricity will shape Uno Minda’s next phase of sustainable and inclusive growth.”
Sunil Bohra, CFO, Uno Minda Group, said, “We are pleased to report a strong start to FY26 with robust top-line and bottom-line performance across key product segments. The 18% year-on-year revenue growth reflects the strength of our diversified portfolio, deep customer relationships, and our continued ability to outperform the industry. Our strategic investments in emerging technologies like EV components, ADAS, sensors, and advanced electronics are beginning to yield tangible results, further strengthening our position as a future-ready automotive solutions provider. As we move forward, we remain committed to disciplined capital allocation, margin stability, and accelerating localisation efforts to create long-term value for all stakeholders.”
Bharat Forge Reports INR 3.39 Billion Net Profit For Q1 FY2026, Maintains Cautious Outlook On US Export Biz
- By MT Bureau
- August 06, 2025
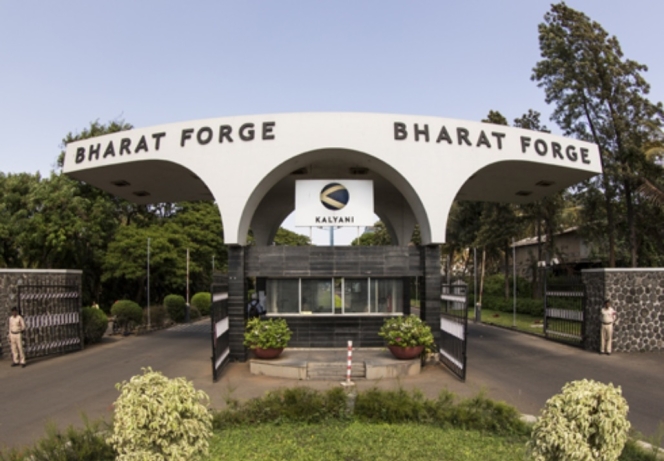
Bharat Forge, a leading engineering and manufacturing company in India, has announced its financial results for Q1 FY2026, which saw its revenue at INR 21.05 billion. The net profit came at INR 3.39 billion, EBITDA at INR 6.82 billion with a margin of 17.5 percent.
The company attributed that it maintained a healthy financial performance despite challenging export market conditions, but resilient performance driven by strong domestic demand and strategic order wins.
During the quarter, Bharat Forge secured new orders worth INR 8.47 billion, which includes INR 2.69 billion from Defence business.
Baba Kalyani, Chairman and MD, Bharat Forge, said, “During the quarter, the company secured new orders worth Rs 847 Crores including INR 2.69 billion in Defence. As of Q1FY26, the defence order book stood at INR 94.63 billion. For the defence vertical, based on the project / platforms we have participated in, we expect to secure new orders in this fiscal year generating more revenue visibility for the future years.
The US & European operations witnessed meaningful improvement in financial performance in the Apr – Jun quarter and are generating cash profit. Review of the European steel manufacturing footprint is on track, and we expect to have concrete steps in place by the end of this year. Given the recent tariff announcement by the US government and changes to emission regulation in North America, we are cautious on the outlook for the US export business for the reminder of the fiscal. FY26 is likely to be a challenging period, given where we are in the overall cycle and our geographical exposure. Our focus is on capturing opportunities in businesses & geographies which are relatively unaffected and work simultaneously on cost optimization to minimize impact of operating deleverage.”
The company stated that despite headwinds from tariff and regulatory uncertainties in key export markets, it continues to strengthen its position through targeted diversification and operational efficiency.
- Tata AutoComp
- Ichikoh Industries
- Valeo
- Valeo Lighting Systems
- Valeo India
- Arvind Goel
- Manoj Kolhatkar
- Christophe Vilatte
Tata AutoComp, Japan’s Ichikoh To Focus On Automotive Lighting Business In India
- By MT Bureau
- August 05, 2025
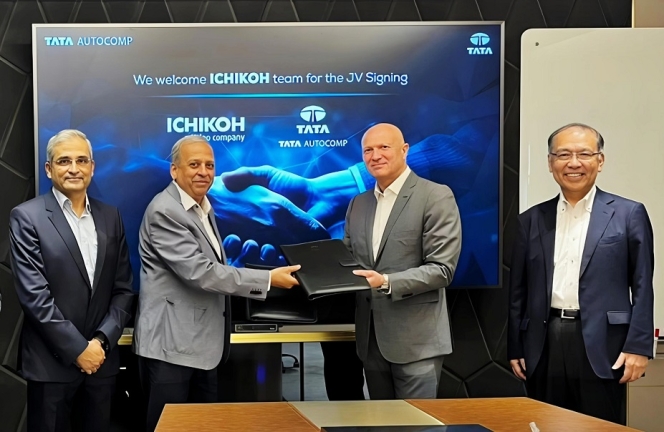
Tier 1 automotive component supplier Tata AutoComp Systems (TACO) has joined forces with Japan’s Ichikoh Industries (Ichikoh) to cater to the automotive lighting market in India. Ichikoh is listed on the Tokyo Stock Exchange Prime Market, wherein Valeo holds a 61.2 percent stake in the company.
As per the understanding, Tata AutoComp Systems and Ichikoh form a JV to acquire Valeo’s lighting business in India will see the partners acquiring Valeo Lighting Systems (VLS) business of Valeo India.
Arvind Goel, Vice Chairman, Tata AutoComp, said, “The formation of this Joint Venture would be another significant step by Tata AutoComp in offering contemporary products and technologies to automotive OEMs in India. We are pleased to welcome Ichikoh and the Valeo Group as our partner, and together with their automotive lighting expertise, we will offer technologically superior and differentiated lighting solutions to our customers.”
Manoj Kolhatkar, MD & CEO, Tata AutoComp, added, “The proposed Joint Venture will enhance our presence in the Indian automotive market and would enable us to serve various OEMs. This collaboration marks another milestone in Tata AutoComp’s journey of offering a comprehensive portfolio of auto-component products.”
Christophe Vilatte, Representative Director, President and CEO, Ichikoh, said, “Ichikoh, with more than 120 years history of technological excellence, will join forces with a new
partner Tata AutoComp, strongly established with its reputational excellence. Capitalising on our respective strength, we will be well positioned to address the fast-growing automotive market in India.”
Comments (0)
ADD COMMENT