- Hindalco Industries
- Aditya Birla Group
- Aluminium
- Copper
- Specialty Alumina
- Kumar Mangalam Birla
- Satish Pai
- electrification
- lightweighting
Hindalco Industries Unveils New Brand Identity, To Invest INR 450 Billion Too
- By MT Bureau
- March 20, 2025
Hindalco Industries, the metals flagship company of the Aditya Birla Group, has unveiled its new brand identity, which it shared marks its transformation from a materials supplier to an engineered solutions provider.
The new identity represents its focus from just being a supplier of metals to a partner with a focus on closing the ecosystem loop right now from sourcing, refining, co-developing and recycling. The company has also outlined an ambitious INR 450 billion towards strengthening aluminium, copper and specialty alumina business.
In an event held in Mumbai, the company displayed its new range of solutions targeted for various industries including B2C, B2B and even B2G. For the automotive industry the company is looking to work together with automakers and suppliers, especially supporting the transition towards lightweighting vehicles and electrification.
Interestingly, the company has also commenced what it claims is India’s first e-waste recycling plant by Birla Copper and a 100MW renewable energy project in Odisha.
Kumar Mangalam Birla, Chairman, Aditya Birla Group unveiled the new identity and said, “Today, Hindalco is a mini conglomerate in itself, with 52 plants across 10 countries producing a diverse portfolio of high-quality products that contribute to the global economy. We are committing INR 450 billion across aluminium, copper and specialty alumina businesses to deliver both upstream and next-generation high-precision engineered products”.
“Hindalco’s new identity reflects our role as a catalyst for change, a problem solver and a co-creator of new solutions that power progress across industries. And above all, it embodies our commitment to always being a force for good,” added Birla.
The new logo features a bold and dynamic ‘H,’ which the company shared represents forward momentum and reinforces its role in shaping India’s industrial and sustainable future.
Satish Pai, MD, Hindalco Industries, added, “This marks a pivotal moment in Hindalco’s journey as we transition from a metals manufacturer to an innovation-driven solutions provider. Our investments in advanced materials, circular economy solutions, and cutting-edge applications will redefine manufacturing in India and beyond. The new brand identity, Engineering Better Futures, reflects our core principles: Sustainability, Circularity, Durability and Precision Engineering. These pillars form the foundation of our transformation, ensuring we create a lasting impact for generations to come.”
China’s NIO Surpasses 800,000 Vehicle Production Milestone
- By MT Bureau
- July 28, 2025
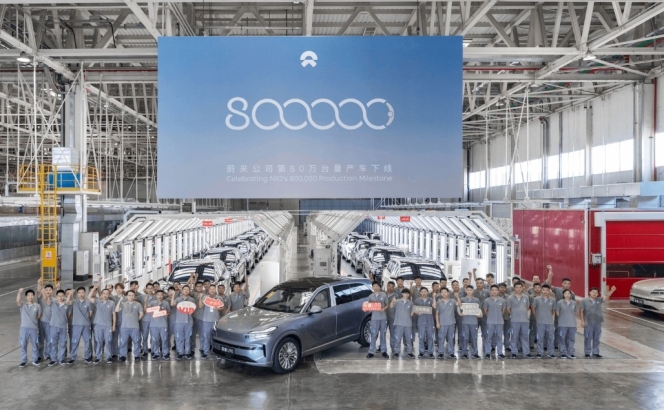
Chinese electric vehicle manufacturer NIO has attained a new production milestone with the 800,000th unit – Onvo L90 – rolling out from its Factory One in Hefei on 24 July 2025.
Since the pre-order started on 10 July, the company shared that the L90 has received widespread interest and recognition from users and the market.
Built on NIO’s decade of investment in the charging and swapping infrastructure, the L90 redefines the family-oriented three-row electric SUV by tackling two major user pain points: charging anxiety and space anxiety.
The test drives for the L90 officially began on 23 July with nearly 600 test drive cars now available at over 400 ONVO stores and showrooms in 140 cities in China. The L90 is set to be officially launched on 31 July, with deliveries starting 1 August.
- Association of Indian Forging Industry
- AIFI
- Bureau of Energy Efficiency
- BEE
- Assistance for Deployment of Energy Efficient Technologies in Industrial Establishments
- ADEETIE
- Yash Munot
- Deven Doshi
- Manohar Lal
AIFI and BEE Sign MoU to Advance Energy Efficiency in Forging Sector
- By MT Bureau
- July 21, 2025
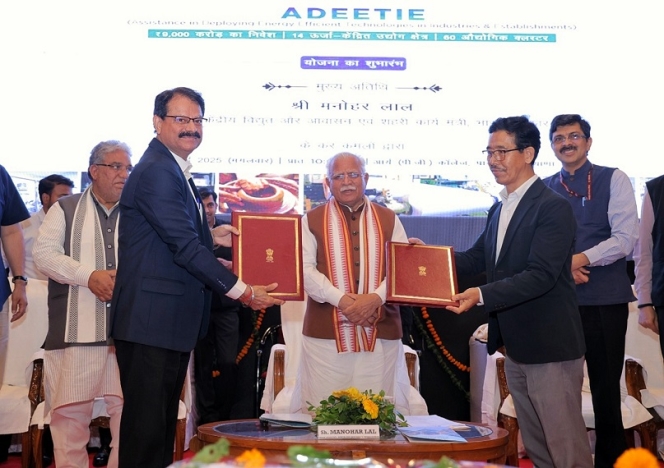
The Association of Indian Forging Industry (AIFI), the apex representative body of the Indian forging sector, has signed a Memorandum of Understanding (MoU) with the Bureau of Energy Efficiency (BEE), Ministry of Power, Government of India.
The agreement was signed in the presence of the Union Minister of Power and Housing & Urban Affairs, Manohar Lal, signifying an important step towards embedding sustainable manufacturing practices within the forging sector. It forms part of the newly launched Assistance for Deployment of Energy Efficient Technologies in Industrial Establishments (ADEETIE) scheme.
The ADEETIE initiative, announced by the Ministry of Power and managed by BEE, is focused on enabling micro, small and medium enterprises (MSMEs) across 14 energy-intensive sectors – including forging – to adopt advanced energy-efficient technologies. The scheme adopts a comprehensive approach, offering:
- Interest subvention on loans for technology adoption (5 percent for micro and small enterprises, 3 percent for medium enterprises).
- End-to-end support, including investment-grade energy audits, guidance with project execution and robust post-deployment monitoring.
- Establishment of a dedicated project management unit and a nodal banking partner to streamline the process.
With a total budget of INR 10 billion, the scheme aims to unlock more than INR 90 billion in overall investments, including INR 67.5 billion specifically set aside for MSME lending. This allocation is expected to reduce the financial burden for forging units seeking to embrace energy-efficient solutions.
Yash Munot, President, AIFI, said, “This collaboration with the Bureau of Energy Efficiency marks a significant step forward for the Indian forging industry. As one of the most energy-intensive sectors, forging stands to benefit immensely from the structured support offered under the ADEETIE scheme. By enabling access to financial incentives and technical guidance, this initiative will empower MSMEs to adopt cutting-edge, energy-efficient technologies. It aligns perfectly with our vision of building a globally competitive, environmentally responsible and innovation-driven forging ecosystem. AIFI is committed to mobilising our members across clusters to take full advantage of this opportunity and contribute meaningfully to India’s broader sustainability and industrial growth goals”.
Deven Doshi, Chairman – Government Interface, AIFI, added, “Energy efficiency is very essential for forging companies, but the MSME sector often faces structural barriers in adopting cleaner and more efficient technologies. The ADEETIE scheme provides a structured framework of support, including technical, operational and financial aspects, that directly addresses these challenges. AIFI is proud to be a partner in this transformative journey. This collaboration not only ensures sectoral compliance with energy norms but also paves the way for long-term industrial modernisation.”
The Indian forging industry, particularly its MSME segment, has been a foundation for the country’s manufacturing and export sectors, supporting diverse areas such as automotive, defence and capital goods. Despite this, the sector has historically faced high energy costs and sustainability challenges. The ADEETIE scheme is set to address these issues directly, equipping forging enterprises with fiscal support and technical know-how to achieve sustainable growth.
Through this MoU, AIFI will actively promote and facilitate the implementation of the ADEETIE scheme across forging clusters nationwide, ensuring that members gain timely access to tools, knowledge, and incentives needed to strengthen both competitiveness and environmental responsibility.
Nissan To Shut Oppama Plant In Japan, Shift Production To Kyushu Facility As Part Of Restructuring Plan
- By MT Bureau
- July 16, 2025
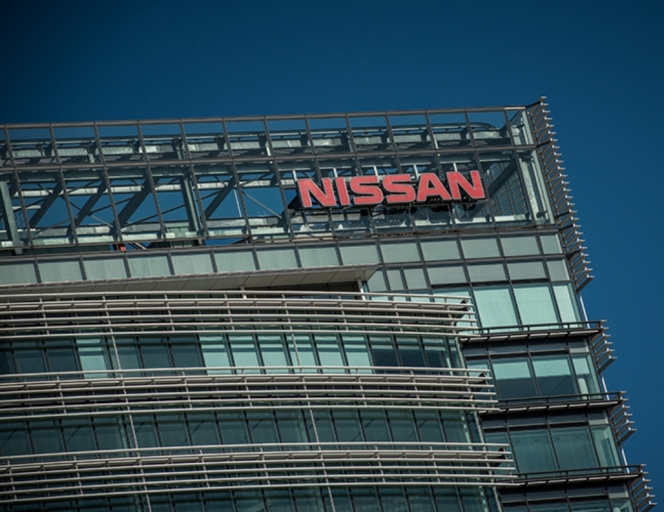
Japanese automaker Nissan Motor Co., which has been undertaking significant measures to improve its financial performance and is restructuring global operations, has announced that it plans to transfer and integrate vehicle production at the Oppama Plant, located in the Oppama district, to Nissan Motor Kyushu Co., Ltd in Fukuoka Prefecture.
This move part of the ‘Re:Nissan’ recovery plan aims to reduce its global production capacity from 3.5 million units (excluding China) to 2.5 million units, while maintaining a plant utilisation rate of around 100 percent. To achieve this, the company has been considering the consolidation of production sites from 17 to 10.
Nissan Reiterates Commitment For India, Targets 200,000 Unit Sales For FY2026
The new announcement will see vehicle production shutting down at Nissan’s Oppama plant at the end of fiscal 2027. Following this, both current and future models scheduled for production at Oppama will be manufactured at Nissan Motor Kyushu.
On the other hand, facilities and functions in the district – such as the Nissan Research Center, Grandrive, the crash test facility and Oppama Wharf – will remain unaffected and continue operations as usual.
Ivan Espinosa, CEO, Nissan Motor Co, said, "Today, Nissan made a tough but necessary decision. It wasn’t easy – for me or for the company – but I believe it’s a vital step toward overcoming our current challenges and building a sustainable future. The Oppama Plant is a proud part of our history, and its legacy will endure. I want to sincerely thank our employees, the local community, and our partners who have supported this plant with dedication and heart. We will continue to operate in the Oppama area with strong support for the local community, as we carry forward the spirit of Oppama plant and work to restore Nissan’s true value."
While the company has announced the shutdown of manufacturing operations at the Oppama plant, it is still exploring a ‘wide range of options to determine the most appropriate path forward’.
The company will continue to retain employees at the plant till the end of fiscal 2027 and is looking to initiate discussions with the union on the future course of action.
Furthermore, the Japanese automaker has also announced that production of the NV200, currently consigned to the Nissan Shatai Shonan Plant, will end in fiscal year 2026. A successor to the NV200 is planned for introduction in fiscal year 2027, with further details to be shared at a later date.
With this decision, Nissan said it has concluded all vehicle production consolidation actions in Japan under the Re:Nissan plan.
Also read: Nissan Secures $6 Billion Through Bond Issuance
- Skoda Auto Volkswagen India
- Skoda India
- Octavia
- Laura
- Superb
- Kodiaq
- Kushaq
- Slavia
- Kylaq
- Andreas Dick
- Piyush Arora
Skoda Auto Volkswagen Rolls Out 500,000th Made In India Skoda Car
- By MT Bureau
- July 04, 2025
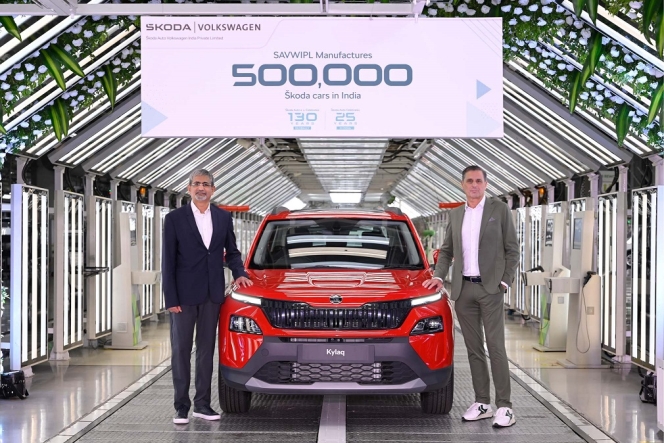
Skoda Auto Volkswagen India has announced that it has achieved a major manufacturing milestone in its operations. The company recently rolled out its 500,000th made-in-India Skoda vehicle.
The milestone comes after 24 years since the company introduced the first Skoda Octavia from its Chhatrapati Sambhaji Nagar facility (formerly Aurangabad) in 2001.
At present, the company manufactures vehicles across two facilities in India – Chhatrapati Sambhaji Nagar and Pune, with them now supporting the company’s new manufacturing plant in Vietnam with parts and components.
Over the years, Skoda has rolled out its iconic products such as Octavia, Laura, Superb and Kodiaq to new products like the Kushaq, Slavia and its first sub-4-meter Kylaq.
Andreas Dick, Board Member for Production and Logistics, Skoda Auto, said, “Reaching the milestone of 500,000 cars produced in India is a proud testament to our strategic vision of unwavering commitment to India and operational excellence. By nurturing local engineering talent and embedding global manufacturing processes, we’ve built an ecosystem that is agile, scalable, and responsive to a dynamically changing environment that meets the highest international standards. This achievement reflects the synergy between world-class innovation and India’s growing industrial prowess.”
Piyush Arora, CEO & Managing Director, Skoda Auto Volkswagen India, said, “It is not just about manufacturing 500,000 cars, but building and nurturing 500,000 connections. Every car that rolls out of our production lines, shares DNA of European engineering with unmatched quality, crafted with precision; delivering supreme comfort, safety, technology and driving dynamics. This achievement belongs as much to our customers as it does to our employees. Because what we’re manufacturing here isn’t just mobility, it’s a belief in what India can make for domestic as well as international markets. India plays a pivotal role in the Group’s growth strategy. I am glad to mention that we achieve this manufacturing milestone in the same year as Skoda Auto celebrates 130 years of legacy globally and 25 years of presence in India.”
The company revealed that approximately 70 percent of the vehicles manufactured in India were rolled out from its Chhatrapati Sambhaji Nagar plant.
Comments (0)
ADD COMMENT