Hyundai Motor India’s Manufacturing Excellence Turns Metal To Marque Cars
- By 0
- April 05, 2020
HMI has 2 plants, established in 1998 and 2007. In the last 5 years both the plants have been augmented for capacity enhancement. This was possible as the assembly lines were initially designed for flexibility in augmentation, expanding to the needs of the following 15-20 years. That has always been the philosophy of Hyundai which is really paying off now; it becomes easier to execute improvements in all their projects.

Consider the body shop where components are accumulated to be worked upon. It is built on global bodyline concepts. Not only volume escalation but also increase in the number of models can be managed effectively. Every day the plant processes 395 tonne of steel coils, globally monitored by ‘Die Management’ system, to make cars with each one having on an average 4,500 spot weldings done by 4th gen robots. So far the company has manufactured more than 9 million cars using steel coils having a length that could cover the circumference of the earth 4 times. The intelligent weld management system generates about 30.6 million data points per day and the quality is controlled through real-time monitoring. Beginning with making one car every 4 minutes in 1998, the plant currently rolls out a car every 33 seconds.
Ganesh Mani S, Director, Manufacturing, HMI, told Motoring Trends that “we have 12 models now with 350 internal variants. The complexities in these are double challenges for us especially when we take to the next level. We were able to manoeuvre 3 or 4 models 3-4 years ago from a single line. Now it is 7 models. Volumes have also increased from 49 to 66 UPH (unit per hour). We have a two-pronged strategy; one is adding on volumes that can cater to the needs of consumers and, two, the capability for enhancement. Since we have our own Factory Automation companies in the automotive hub of South Korea, we have gone from Generation-1 to Generation-4 of robotics, which brings in a certain amount of flexibility and increase in the speed of execution. With CAFE and other norms, we need to make a model that is robust, which comes from the basic design and the way we build the product.”
Body shops are by and large 100 percent automated and therefore, the company was able to make them intelligent enough to understand, with the fourth generation robots. For every vehicle it is necessary to have resistant spot welding and for every spot there is a specification; this needs to be modified for each new model. The company has introduced intelligent timer controls, which is called MMDI - in the line before spot welding, it checks the number of components and their thickness and the level of current and voltage requirements.
Earlier they were pre-set, but now keep changing at every place. This gives twin advantages. The first is to have multiple components as technologies keep changing; aluminium may come in; high tensile steel welding has already come. At present the plant has about 400 robots with MMDI which have the capability to keep checking every time. Earlier it used to take 40 seconds to complete 30 spots; now within that TAKT time, it is able to make 50 spots increasing the speed of the line.
The second is having Intelligent Vision Control Systems. For instance, sealer has to be applied for vibration, harshness, noise, dust and rust prevention, strength, etc. The system monitors the route it has to follow and checks whether the job is being done properly or not. It ensures quality and traceability of the arrangement.
“Whenever we introduce a new model all we have to do is to make use of the carrier, a hardware that allows robots to move around and make the body parts. Only the carriers need to be replaced as the line operates depending on the types to be made. Earlier we had electric and pneumatic carriers to move across to lift the body and components while in the fourth generation robots at present the individual carrying capacity has been increased multiple times. The entire handling mechanism of conveyors, platforms, holding chains, etc has been replaced by just programming the robots which can handle them. All these save time and make the operation of the body shop more convenient,” he said.
A robot has shelf life of approximately 7 years; as and when replacements are due, new technologies are incorporated into the system. With so much innovation in robotics, the cost of robots is going down. Over the years the company has garnered expertise to the extent that a new robot can be commissioned in 48 hours, when it is needed to augment capacity. The industry average is 7 or 8 days. The supervisors and technicians can do the programming themselves, which also saves cost. Assembly shops have seven or eight major equipment and the company has been able to change or enhance the equipment that is augmented with VFD (variable frequency drive) as and when required. A fall back mechanism is in place to manage demand fluctuations. Robotic multi-skills and flexibility switchover help the line to go on smoothly. When not required some of the robots can be kept in sleep mode to save energy. Like managing absenteeism of people with multi-skills some of the robots can double up while the others can rest.
On the scope for improvement in enhancing UPH, Ganesh Mani said, “We can manage with this arrangement till 2021. We change regularly our upgradation on various models and try to eliminate defects at the design stage itself. We have a team working on every model and the results are ploughed back at the design stage to remove deficiencies. Also, there is the influx of technology in terms of inspection and robustness of the process. ‘Before’ and ‘After’ is 100 percent mapped for the sealers so there is no question of missing and moving across to the next stage.”
In the body shop the operator has all the available information in front of him. In the assembly shop everything is mapped digitally. The operator looks at a digital display to know which component he has to pick up; he also gets an audio message regarding assembly of parts for rare models. The company has created a Smart Innovation and Automation Team (SIAT) which is one step ahead in process monitoring to ensure that errors do not creep into the system; it makes certain that the operator does not commit a mistake. For instance the lid of containers holding the parts for the specific models will only open when required and at the right station.
Asked what happens if the operator has not taken the required number of parts like fasteners, he said, “We have more than 700 dynamic bolts and nuts that are fitted on the vehicle; any mistake in fitment would create havoc. We have HIVIS (Hyundai Integrated Vehicle Inspection System) which is a tool by itself. The torque values while tightening every nut are registered in the system. Any mistake made triggers an alarm and the vehicle will not be allowed to go to the next stage. The tightening process is monitored in real-time and is coupled with sign-off gate. When there is a process deviation, the system will not allow the car to roll out of the assembly line, thereby ensuring mistake-proof delivery. The system, developed at HMIL, is so intelligent that it is used all over the world. For example, when new trainees come, sometimes cross-threads happen; the torque goes very high and the value is reflected in the torque curve. This helps us take immediate corrective action. One of our engineers developed a ‘gyro metric gun’ that works on the straightness principle. It has a sensor inside, working on the principle of gravitational force; if there is any deviation of line it will not allow the operator to tighten the nut. This is a unique system, being used in all the 32 plants of Hyundai globally.”
How can variability happen? It can happen because of improper training; the company has taken care of this. The other variability is fatigue that could set in and result in the operator making a mistake. To prevent this there is REBA - Rapid Entire Body-movement Analysis - that can calculate the fatigue level in the individual. This information would help improve his comfort level. Meticulous planning has been done for all the stations, upgrading them from category A (with possibility of over 12 risk occurrences) to category D (less than 4), to bring down the risk level. On this platform there are many assist systems for the operator. The company is working on EXO skeleton which is a human-machine interface where a vest is provided to the operator giving him, among other things, elbow support. This makes the process easier and lighter; consistency always gets measured.
Ganesh Mani explained, “We also have vision camera system robotics that can capture 70 frames per minute. It compares the pictures with the original and if there is an error sends the message within a TAKT time of 40 seconds. This is our third layer of inspection. By and large our pass ratio is 100 percent; it is only a fall-back mechanism.”
Though the number of models assembled in one line has substantially increased, the company hopes that it can increase further. In assembly, there can be a high of as many as 240 different models, the maximum in a single line, he pointed out.
However, when the UPH in the body shop is increased it has to match the TAKT time of the assembly line as well. “In a lean production system we don’t want too much of a cushion in the other shops as that would prevent hidden problems from coming out. So we don’t go beyond one additional UPH in the previous shop; in between we have some amount of stock for body storage. Within that we manage our line. Every hour the body shop can create 1 more additional body in the same time required for assembly. In this way we can manage any breakdown or process delay up to 1 UPH. On a cumulative of 22 hours that we run, everyday a cushion of 22 bodies will be available to help us manage any kind of change,” he said.
Industry 4.0
About the possibilities of a smart factory Ganesh Mani said, “As part of our agile manufacturing process in our technologically advanced and digitalised factory we wanted to use Industry 4.0 in a big way. Our initiatives for this have started. We have found out that earlier in a body shop alone close to 1GB of data was generated; today it is 15GB a year from all the modules put together. The next stage is to integrate the data seamlessly and put them on display so that the operator who is multi-tasking can see them easily and monitor them thoroughly. This also helps in predictive maintenance which is the objective of big data. We use this in a 6-8 hour slot on Sundays when the assembly line does not work. Any change can be made then. This phase pre-empts impending failures; we use infrared mechanisms to do this. We also have vibration sensors fitted in the equipment that constantly monitor and give an alarm if something is likely to happen like heating up of the motors. We have a Data Analytics Team that looks into all these and takes preventive action. Today, more than 50 data scientists are working on the shop floor. By 2021 we want to integrate all the shops through this process so that we can predict what could happen. An example of how digitalisation in Industry 4.0 is helping us is in the breaking of equipment; whenever the vacuum levels start going up, the machine stops. To avoid this, by digitalisation we can constantly monitor the control limits to ensure that the equipment works in the programmed range. If it goes beyond the safe level, the system sends an SMS to the maintenance team. This helps the operator to plan and change the machine to a new area.”
Energy Conservation
HMI has completely switched over to LEDs, saving about 40 percent energy required for lighting. “Within 18 months we were able to get back the cost of the whole system. We always ensure that energy efficient motors are used. We are also very careful in using water, especially in places like Chennai where water is scarce. We are into hundred percent rain water harvesting. One mm of rain means a saving of 750 kl of water throughout the plant. We can manage 150 days of production without water from other sources; we are planning for complete independence,” he said. (MT)
Skoda Teases New Vision O Concept Interior
- By MT Bureau
- August 25, 2025
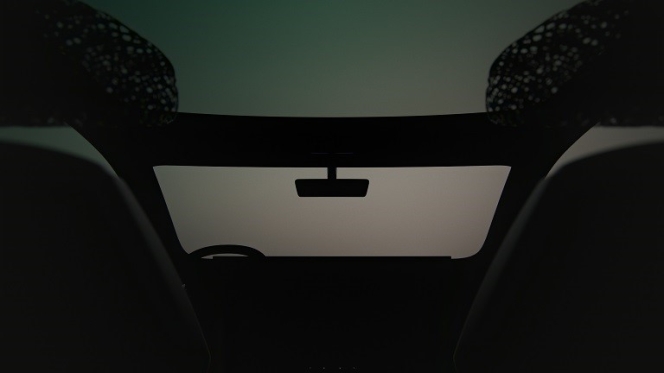
Skoda has released a teaser video offering the first look inside its upcoming Vision O concept car, revealing a new interior design language. The car will be officially unveiled on 8th September in Munich.
The interior showcases the next evolution of the brand’s Modern Solid design philosophy, focusing on a customer-centric and sustainable approach. The design emphasises a spacious layout with clean lines for a harmonious feel.
Oliver Stefani, Head of Skoda Design, said, “The interior design concept of the Vision O showcases our commitment to combining simplicity and sustainability with enhanced comfort. The combination of clean lines and intuitive functionality reflect our efforts to create a harmonious and functional interior. It features materials and design elements that are not only aesthetically an evolution of our Modern Solid design language but also emphasise environmental responsibility.”
The interior features a minimalist, ergonomic design that prioritises practicality and intuitive functionality. It includes unique 3D-printed headrests for a comfortable and airy feel. Following circular economy principles, the materials used throughout the cabin are sustainable, with a focus on plant-based and compostable components to reduce the car’s environmental impact.
The Vision O will be a look at the future of Skoda’s estate segment.
Renault Launches New Kiger SUV At INR 629,000
- By MT Bureau
- August 24, 2025
Renault India has released the new Kiger, an updated version of its sub-four-meter SUV at prices starting INR 629,000 with prices going upto INR 1.12 million (ex-showroom).
The SUV is an evolution of the previous model, features over 35 updates. It was developed to align with the ‘rethink performance’ philosophy.
The new Kiger has a refreshed exterior and an updated interior. It now includes a multi-view camera system, rain-sensing wipers and automatic headlamps. The Kiger is also equipped with a 20.32 cm touchscreen and a sound system.
The Kiger is available with two engine options: a 100 PS turbocharged engine and a 72 PS naturally aspirated engine. For safety, the new Kiger offers 21 standard safety features across all versions, including six airbags, ESP and Hill Start Assist.
Venkatram Mamillapalle, MD and CEO, Renault India, said, “We are excited to launch the New Kiger in a segment which is growing fastest and contributes 50% to the SUV sales and 31% to the TIV of the country. Kiger has been a unique product in its segment, and with this latest evolution, we are reaffirming our commitment to making expressive design, intelligent engineering, and real-world performance accessible to Indian customers. This marks a pivotal moment in Renault’s India centric transformation journey renault. rethink.”
Francisco Hidalgo, Vice-President, Sales and Marketing, Renault India, said, “Renault Kiger has shaped expectations in the compact SUV segment with its aesthetic design, modern details, and bold stance combined with the lightweight CMFA+ platform. The New Kiger remains highly agile and responsive, giving customers the confidence of SUV DNA with the ease of everyday driving on city roads and highways- ticking all that is required for perfect performance.”
Hyundai Exter Gets New Pro Pack, New Colour Options & Features
- By MT Bureau
- August 22, 2025
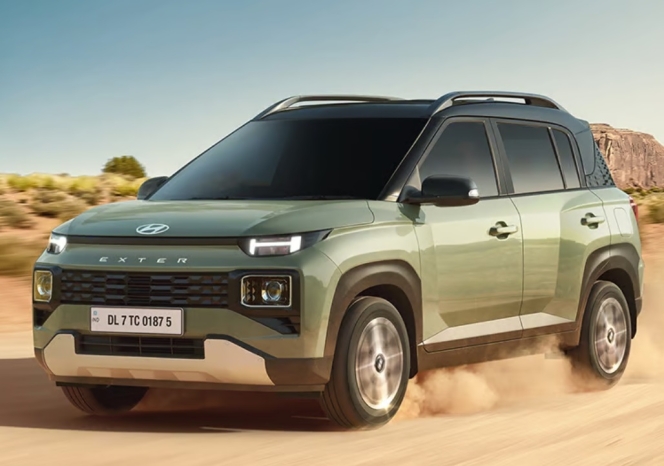
Hyundai Motor India (HMIL), one of the leading passenger vehicle manufacturers, has introduced ‘PRO’ Pack in its popular compact SUV the Hyundai Exter at starting price of INR 798,390 (ex-showroom).
The new Pro pack features wheel arch cladding, side sill garnish, all-new Titan Grey Matte colour and a Dashcam to make the SUV more safer.
Tarun Garg, Whole-Time Director and Chief Operating Officer, Hyundai Motor India, said, "At HMIL, we are continuously evolving our product offerings to resonate with the aspirations of today's young and progressive customers. The introduction of PRO Pack in Hyundai EXTER is a step further in this direction, combining bold styling, advanced technology and strong safety to create a truly distinctive value proposition. With its refreshed appeal, the PRO Pack in Hyundai EXTER strengthens our commitment to redefining customer delight and making every drive a PRO experience."
MOL, Suzuki Motor Corporation And TradeWaltz Join Forces To Decarbonise Automobile Trade Between India & Africa
- By MT Bureau
- August 22, 2025
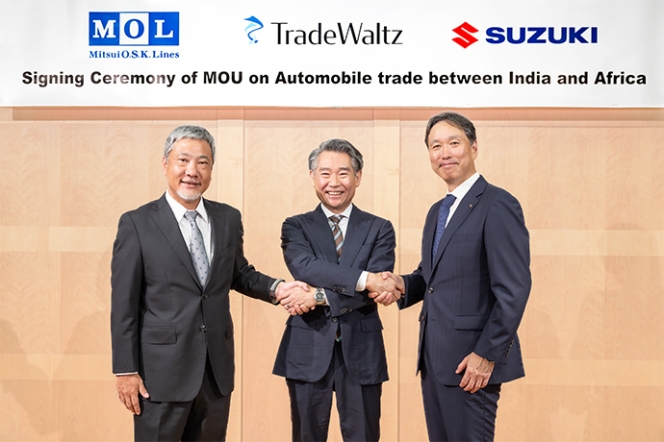
MOL, Suzuki Motor Corporation and TradeWaltz have announced a new partnership to streamline and decarbonise the automobile trade between India and Africa. The three companies signed a memorandum of understanding (MoU) at the 9th Tokyo International Conference on African Development (TICAD 9) in Yokohama.
This collaboration aims to address current challenges in the trade by leveraging digital solutions and enhancing efficiency. The companies will focus on identifying problems in the supply chain and developing solutions for smoother transportation. A key part of the initiative is also promoting decarbonisation efforts within the logistics process.
The partnership aligns with the ‘Japan-India Cooperation Initiative for Sustainable Economic Development in Africa,’ launched in February 2025. By combining their individual strengths, MOL, Suzuki and TradeWaltz hope to contribute to the economic development of both India and Africa. The companies stated that this MU is the first step toward building a more robust and interconnected automobile supply chain between these two rapidly growing markets.
Comments (0)
ADD COMMENT