Yamaha’s Chennai Factory Marks a Decade of Manufacturing Excellence
- By MT Bureau
- June 04, 2025
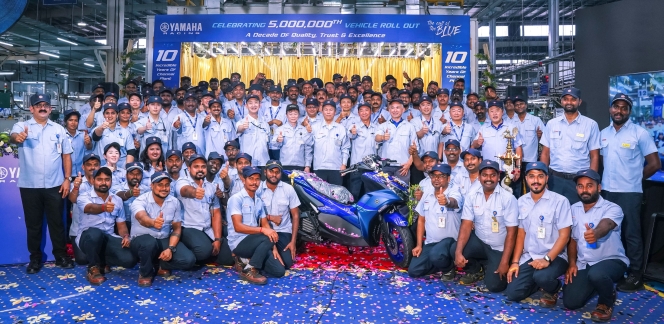
India Yamaha Motor (IYM) Pvt Ltd has achieved a significant milestone in its manufacturing journey with the completion of 10 years of operations at its Chennai Factory. Reinforcing its role as a critical production base for both domestic and global markets, the company also celebrated the roll-out of its five millionth two-wheeler from this state-of-the-art facility—an Aerox 155 Version S that marked the milestone.
Over the past decade, the Chennai plant has become a cornerstone of Yamaha’s global operations to serve both Indian customers and export markets. It currently manufactures Yamaha’s hybrid scooter range including the RayZR 125 Fi and Fascino 125 Fi, along with the performance-oriented Aerox 155 Version S. From an export standpoint, the facility also produces the FZ series, the Saluto range, and the Alpha scooter—reinforcing the factory’s role in delivering Yamaha's trusted quality to diverse global markets. More than 30% of the factory’s total output is exported, reflecting its manufacturing strength and global relevance.
Speaking on the occasion, Itaru Otani, Chairman, Yamaha Motor India Group of Companies, said, “The Chennai factory holds strategic importance in Yamaha’s global manufacturing network. It exemplifies our unwavering focus on people, processes, and products—driven by skilled employees, synchronized operations, and a strong commitment to global quality standards. As one of Yamaha’s most modern manufacturing facilities worldwide, it has supported India’s mobility aspirations while reinforcing its role as a trusted exporter to global markets. As we celebrate the roll-out of the 5 millionth two-wheeler, I extend my deepest appreciation to our dedicated employees, vendor partners and passionate customers who have made this journey possible. We will continue to progress, and Chennai factory will keep playing a major role in addressing the evolving customer demands in Indian and overseas markets.”
Spread across 177 acres, the Chennai factory operates with a unique integrated model—109 acres dedicated to IYM and 68 acres to co-located vendor partners—enabling seamless synchronization under a unified ‘One Factory’ concept. This approach has enhanced manufacturing efficiency, speed, and supply chain integration, making the facility one of Yamaha’s most advanced in the world.
Over the last decade, the Chennai manufacturing facility has been consistently upgraded to support Yamaha's evolving premium product strategy—producing high value-added motorcycles and scooters with small to midrange engine displacements. With India’s stringent emission regulations, Yamaha Motor Company Ltd. identified an opportunity to position this plant as a global export hub, delivering products that meet the highest standards of performance and compliance. Today, the factory supports Yamaha’s portfolio across segments—ranging from premium models for Indian customers to those tailored for markets in Europe, Latin America, ASEAN, and beyond. With its focus on quality, digital systems, and sustainable technologies, the facility is well-prepared for the future of smart and eco-friendly manufacturing.
Demonstrating Yamaha’s long-standing commitment to sustainability, the plant houses an installed solar power capacity of 4450 kW, significantly reducing its carbon footprint and supporting green manufacturing practices. The facility incorporates state-of-the-art infrastructure and advanced technologies for zero-water discharge and recycle/reuse of wastewater. It is also designed for maximum use of sunlight, and the buildings are compatible with solar power system installation. All common utilities are centrally located to minimize distribution loss and ensure centralized management, making it a model of sustainable industrial planning.
As Yamaha celebrates this dual milestone, the Chennai plant stands as a testament to the brand’s long-term commitment to make-in-India as a strong manufacturing and development hub of world-class two-wheelers. This achievement marks a significant step forward in strengthening Yamaha’s motorcycle business in Indian market with the unwavering support and loyal partnership of our enthusiastic customers who continue to inspire us at every step to push the limits of innovation and performance offering unique and enriching experiences worldwide.
Mercedes-Benz Marks 600,000th G-Class With Electric Model
- By MT Bureau
- August 06, 2025

German luxury carmaker Mercedes-Benz has attained another milestone by rolling out the 600,000th Mercedes-Benz G-Class from Graz, Austria. The milestone vehicle is an electric G 580 with EQ Technology finished in obsidian black metallic.
Since its launch in 1979, the G-Class has become a symbol of off-road capability and design. The first G-Models combined off-road performance with on-road comfort and Mercedes' safety standards. In the past four decades, it has evolved while retaining key features such as all-wheel drive, differential locks, and a ladder frame. Design elements like the round headlights and exposed spare wheel remain.
In celebration of its heritage, a limited edition, the G-Class Edition Stronger Than The 1980s, was released last year. This model paid homage to the original W 460 series.
The brand's customisation service, Manufaktur, has seen increasing popularity. Since 2019, over 90 percent of G-Class customers choose at least one Manufaktur option, averaging three per vehicle. Customers can now select from up to 20,000 paint colours, including heritage shades.
VinFast Inaugurates Tamil Nadu EV Plant
- By MT Bureau
- August 04, 2025
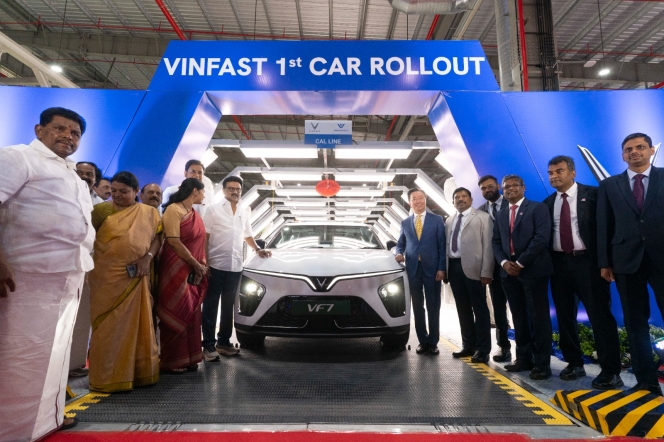
Vietnamese automaker VinFast has officially inaugurated its electric vehicle assembly plant at SIPCOT Industrial Park in Thoothukudi, Tamil Nadu, India.
The new facility is VinFast’s third operational plant and the fifth project in its global manufacturing network. It is part of the company’s long-term bet on selling its vehicle in the world’s third-largest automobile market.
The factory is spread across 400 acres and is equipped with state-of-the-art production lines, featuring advanced automation and technologies. The complex houses multiple workshops, including body shop, paint shop, assembly shop, quality control centre, and a logistics hub. It also includes an auxiliary cluster for local contractors, which is expected to expand in the coming years.
The company expects to create around 3,500 jobs for local workers at full capacity, along with several thousand indirect jobs in the supply chain ecosystem. To start with, the company will assembly the VF 7 and VF 6 electric vehicles with a capacity of 50,000 units per annum, which can be scaled upto 150,000 units per annum to meet market demand.
VinFast states with the Tamil Nadu plant on stream, it moves closer to its 2025 sales target of 200,000 vehicles and its long-term production goal of 1 million vehicles per year by 2030.
Pham Sanh Chau, CEO, VinFast Asia, said, “The VinFast Tamil Nadu plant marks a strategic milestone in our long-term commitment to the Indian market. It establishes a strong foundation for sustainable growth and positions us to offer high-quality, competitively priced electric vehicles to Indian consumers. Looking ahead, the facility will expand its production capacity to meet rising demand. We aim to develop it into VinFast’s largest export hub for South Asia, the Middle East, and Africa. In fact, we've already secured initial orders from several countries across these regions. In close collaboration with the Tamil Nadu government, VinFast is working to transform the area into the 'EV capital of South Asia'—supporting both the dynamic domestic market and our broader regional ambitions.”
Going forward, VinFast aims to further promote localisation, technology transfer and also upskill its workforce.
China’s NIO Surpasses 800,000 Vehicle Production Milestone
- By MT Bureau
- July 28, 2025
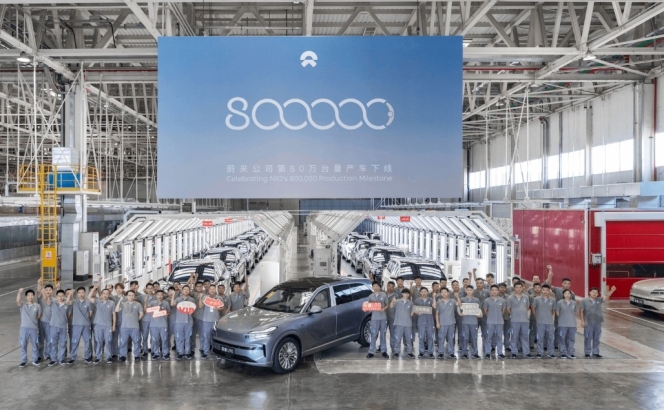
Chinese electric vehicle manufacturer NIO has attained a new production milestone with the 800,000th unit – Onvo L90 – rolling out from its Factory One in Hefei on 24 July 2025.
Since the pre-order started on 10 July, the company shared that the L90 has received widespread interest and recognition from users and the market.
Built on NIO’s decade of investment in the charging and swapping infrastructure, the L90 redefines the family-oriented three-row electric SUV by tackling two major user pain points: charging anxiety and space anxiety.
The test drives for the L90 officially began on 23 July with nearly 600 test drive cars now available at over 400 ONVO stores and showrooms in 140 cities in China. The L90 is set to be officially launched on 31 July, with deliveries starting 1 August.
- Association of Indian Forging Industry
- AIFI
- Bureau of Energy Efficiency
- BEE
- Assistance for Deployment of Energy Efficient Technologies in Industrial Establishments
- ADEETIE
- Yash Munot
- Deven Doshi
- Manohar Lal
AIFI and BEE Sign MoU to Advance Energy Efficiency in Forging Sector
- By MT Bureau
- July 21, 2025
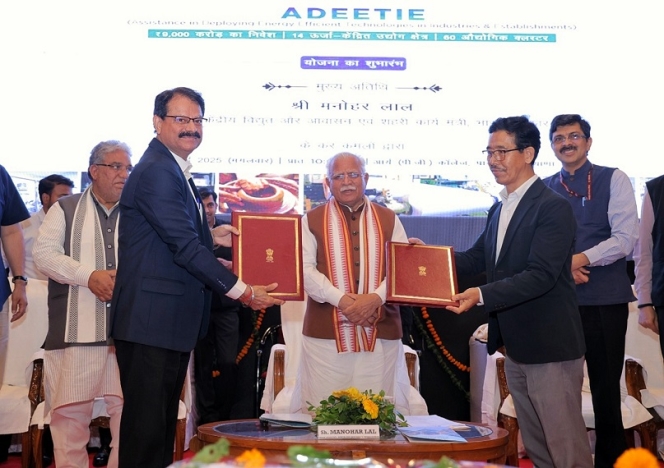
The Association of Indian Forging Industry (AIFI), the apex representative body of the Indian forging sector, has signed a Memorandum of Understanding (MoU) with the Bureau of Energy Efficiency (BEE), Ministry of Power, Government of India.
The agreement was signed in the presence of the Union Minister of Power and Housing & Urban Affairs, Manohar Lal, signifying an important step towards embedding sustainable manufacturing practices within the forging sector. It forms part of the newly launched Assistance for Deployment of Energy Efficient Technologies in Industrial Establishments (ADEETIE) scheme.
The ADEETIE initiative, announced by the Ministry of Power and managed by BEE, is focused on enabling micro, small and medium enterprises (MSMEs) across 14 energy-intensive sectors – including forging – to adopt advanced energy-efficient technologies. The scheme adopts a comprehensive approach, offering:
- Interest subvention on loans for technology adoption (5 percent for micro and small enterprises, 3 percent for medium enterprises).
- End-to-end support, including investment-grade energy audits, guidance with project execution and robust post-deployment monitoring.
- Establishment of a dedicated project management unit and a nodal banking partner to streamline the process.
With a total budget of INR 10 billion, the scheme aims to unlock more than INR 90 billion in overall investments, including INR 67.5 billion specifically set aside for MSME lending. This allocation is expected to reduce the financial burden for forging units seeking to embrace energy-efficient solutions.
Yash Munot, President, AIFI, said, “This collaboration with the Bureau of Energy Efficiency marks a significant step forward for the Indian forging industry. As one of the most energy-intensive sectors, forging stands to benefit immensely from the structured support offered under the ADEETIE scheme. By enabling access to financial incentives and technical guidance, this initiative will empower MSMEs to adopt cutting-edge, energy-efficient technologies. It aligns perfectly with our vision of building a globally competitive, environmentally responsible and innovation-driven forging ecosystem. AIFI is committed to mobilising our members across clusters to take full advantage of this opportunity and contribute meaningfully to India’s broader sustainability and industrial growth goals”.
Deven Doshi, Chairman – Government Interface, AIFI, added, “Energy efficiency is very essential for forging companies, but the MSME sector often faces structural barriers in adopting cleaner and more efficient technologies. The ADEETIE scheme provides a structured framework of support, including technical, operational and financial aspects, that directly addresses these challenges. AIFI is proud to be a partner in this transformative journey. This collaboration not only ensures sectoral compliance with energy norms but also paves the way for long-term industrial modernisation.”
The Indian forging industry, particularly its MSME segment, has been a foundation for the country’s manufacturing and export sectors, supporting diverse areas such as automotive, defence and capital goods. Despite this, the sector has historically faced high energy costs and sustainability challenges. The ADEETIE scheme is set to address these issues directly, equipping forging enterprises with fiscal support and technical know-how to achieve sustainable growth.
Through this MoU, AIFI will actively promote and facilitate the implementation of the ADEETIE scheme across forging clusters nationwide, ensuring that members gain timely access to tools, knowledge, and incentives needed to strengthen both competitiveness and environmental responsibility.
Comments (0)
ADD COMMENT