Optimised Bacalar W12 Engine Delivers Improved Power, Torque
- By T Murrali
- April 11, 2021
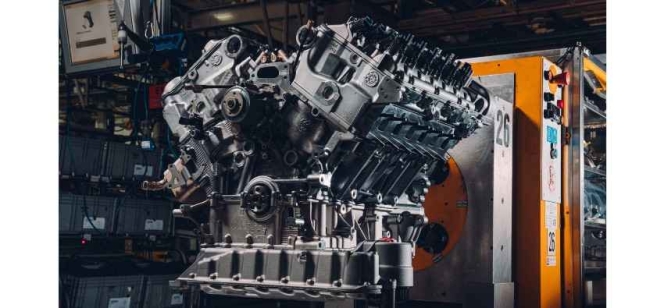
The Bacalar spearheads a return to coachbuilding by Bentley Mulliner and features an enhanced version of Bentley’s peerless 6.0-litre W12 TSI engine, the most advanced 12-cylinder engine in the world.
Since the first introduction of the twin-turbocharger W12 in 2003, the engine’s refinement has seen an increase of up to 27 percent in power, 38 percent in torque and a reduction of 38 percent in emissions.
This has been realised through the evolution and optimisation of the crankcase, improvements in the oil and cooling systems, twin-scroll turbocharging technology and more effective injection and combustion processes.
Sources from Bentley told this correspondent that these improvements resulted from several initiatives taken by the company. It may be recalled that the latest generation of W12 was launched in the Bentayga in 2016. “A thoroughly reworked engine included a crankcase 30 percent stronger than its predecessor, while the cylinder surfaces were coated to reduce friction and improve corrosion resistance. A low-alloy steel coating is applied to the bores using an Atmospheric Plasma Spray (APS) process. Improvements were also made to the cooling system, with the engine featuring three separate coolant circuits. The first is designed to bring the cylinder heads up to optimum operating temperature as quickly as possible for best engine performance and low emissions. The second cool the engine block and oil system, while the third handles the turbochargers’ thermal load. Each system has a dedicated water pump, allowing optimised individual control,” sources said.
Twin-scroll Turbocharging
Twin-scroll turbochargers minimise turbo response time and provide a more efficient exhaust package. The exhaust assemblies for the three front and three rear cylinders are separate from one another, which feed the twin-scroll impellers. The turbocharger housing is welded directly to the exhaust manifolds and feature integrated speed sensors, allowing the engine to monitor turbo performance for maximum efficiency.
Effective Injection
The W12 combines high-pressure direct fuel injection (200 bar injection pressure) with low-pressure port injection (six bar). The combination of these two systems maximises refinement, lowers particulate emissions and optimises power and torque delivery.
Interestingly, each W12 engine is hand-built over 6.5 hours by a team of 45 craftspeople before undertaking a highly sophisticated test regime of over an hour via three specialist diagnostic machines during the engines assemble.
According to the sources, there were three specialist diagnostic machines with sophisticated test regime.
Leak Test
The leakage test is conducted by pressurising each of the systems for fuel, oil and water individually. The different cavities are pressurised to values between 0.2 – 5.0 bar respectively and then measured whilst the pressure decays over time. The reduction in pressure versus time represents the quality of the sealing of the engine assembly. If the pressure drops faster than expected, a leak is indicated. A special fluid is sprayed on to the exterior of the engine to pin-point any leakage paths.
Cold Test
The engine is loaded on to a testbed plate, and connections are made to the engine loom and all engine systems, whilst a large electric motor couples to the engine via the crankshaft. “Motoring” the engine via the crankshaft allows the testbed to collect data from a suite of sensors. The facility measures 600 individual properties and characteristics of the engine during a 15-minute cycle. Due to the low running speed of 120 RPM for the test, finer details and any inconsistencies can be identified thanks to a sample rate that highlights even the briefest of anomalies that would be invisible if the engine was firing or running at speed. This fine detail analysis is also valuable for confirming the precise timing of the engine. Using positioning information from sensors on the crankshaft, crankcase and camshafts, and cylinder compression values, the Cold Test can confirm the engine timing is accurate and, therefore, achieve the best possible combustion cycle.
Hot Test
When the engine arrives for hot testing, a UV dye is added to the engine to help identify any leaks. The coolant and fuel system are pressurised with air and nitrogen, respectively, for a final check before introducing the necessary fluids ready for testing. The engine is cranked to build oil pressure before the ignition system is energised and then left to idle whilst the engine test technician listens for any refinement issues and checks for leaks with a UV lamp. Sources said that each W12 is then tested for a minimum of 21.5 minutes and runs up to 3,800 rpm with a maximum load of 300 Nm. One in every one hundred engines receives a full eight-hour power test, achieving 6,000 RPM, and must achieve 900Nm.
The three tests that the Bacalar engine has already been put through are part of Bentley’s exceptional quality control processes. These testing procedures provide feedback on the quality of each engine and provide multiple checkpoints to catalogue the exact behaviour of each engine from the moment of manufacture. Since the installation of the three testbeds in 2002, over 100,000 W12 engines have been handcrafted in Crewe and passed through the test facility.
Technology Advancements
Bentley’s legendary 6.0-litre twin-turbocharged W12, created in 2002, has evolved into the latest iteration of the W12 engine used across today’s current model range. The unique W-configuration means that the engine is 24 percent shorter than an equivalent V12, benefitting packaging and maximising usable cabin space.
The latest generation of W12 was launched in the Bentayga in 2016. A thoroughly reworked engine included a crankcase 30 percent stronger than its predecessor, while the cylinder surfaces were coated to reduce friction and improve corrosion resistance. A low-alloy steel coating is applied to the bores using an Atmospheric Plasma Spray (APS) process.
The W12 combines high-pressure direct fuel injection (200 bar injection pressure) with low-pressure port injection (six bar). The combination of these two systems maximises refinement, lowers particulate emissions and optimises power and torque delivery.
Twin-scroll turbochargers minimise turbo response time and provide a more efficient exhaust package. The exhaust assemblies for the three front and three rear cylinders are separate from one another, which then feed the twin-scroll impellers. The turbocharger housing is welded directly to the exhaust manifolds and feature integrated speed sensors, allowing the engine to monitor turbo performance for maximum efficiency.
Bentley’s variable displacement system shuts down half of the engine under defined conditions. Intake and exhaust valves, fuel injection and ignition are all shut down on defined cylinders, with the engine running as a six-cylinder for improved efficiency. The system will run in this mode in gears three to eight, below 3,000 rpm and up to 300 Nm torque output.
The first Bacalar engine followed the same build process in Bentley’s centre of excellence for W12 engines, ensuring the same level of quality and expertise before final testing, sources added. (MT)
Sustainable, Recyclable Electric Motors
Bentley Motors has announced a three-year research study that aims to revolutionise the sustainability of electric motors. Supporting Bentley’s commitment to offering only hybrid or electric vehicles by 2026, the result could see recycled rare-earth magnets used in selected ancillary motors for the very first time.
The study, titled RaRE (Rare-earth Recycling for E-machines), intends to build on work completed at the University of Birmingham in devising a method of extracting magnets from waste electronics. The project will also scale up this process and repurpose the extracted magnetic material into new recyclable magnets for use within bespoke ancillary motors.
Adding to the sustainability benefits that RaRE will provide, the bespoke motors created through this method promise to minimise complexity through manufacture while supporting the development of the UK supply chain for both mass production and low volume components.
Dr Matthias Rabe, Member of the Board for Engineering, Bentley Motors, said, “As we accelerate our journey to electrification, offering only hybrid or electric vehicles by 2026, and full electric by 2030, it is important that we focus on every aspect of vehicle sustainability, including sustainable methods of sourcing materials and components. RaRE promises a step-change in electrical recyclability, providing a source of truly bespoke, low voltage motors for a number of different applications, and we are confident the results will provide a basis for fully sustainable electric drives.”
This study will run in parallel to Bentley’s OCTOPUS research programme, which aims to deliver a breakthrough in e-axle electric powertrains, utilising a fully integrated, free from rare-earth magnet e-axle that supports electric vehicle architectures.
As with OCTOPUS, RaRE is an OZEV funded project delivered in partnership with Innovate UK, which brings together the following partners with distinct roles and responsibilities. Bentley Motors will lead specification setting and test protocol development and support the design and manufacturing activities, while Hypromag will scale up the recycling processes developed at the University of Birmingham and convert the extracted powders to sintered magnets with properties designed around those required for the auxiliary motors. On its part, Unipart Powertrain Applications Ltd will lead the development of manufacturing scale-up routes to ensure facilities and processes defined are suitable for volume automotive manufacture.
Advanced Electric Machines Research Ltd will lead the motors’ design and development, while Intelligent Lifecycle Solutions Ltd will pre-process computer hard disk drives to remove the rare earth magnet containing components from the waste, which will be shipped to Hypromag for removal of the rare earth magnets. The University of Birmingham will provide cast alloys, which will be fed into Hypromag to blend with secondary materials to produce sintered magnets. (MT)
Maruti Suzuki India Marks 10 Years Of Nexa With Grand Vitara Phantom Blaq Edition
- By MT Bureau
- August 10, 2025
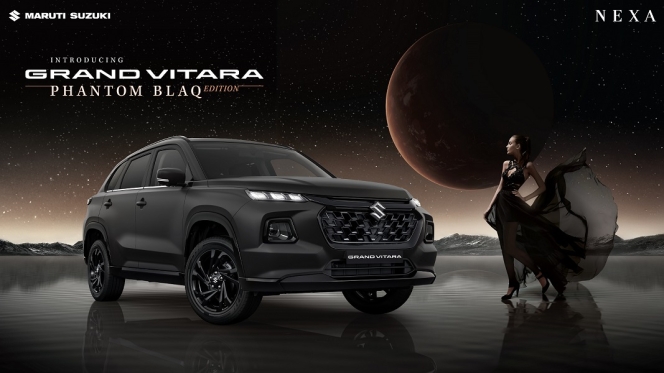
Maruti Suzuki India is commemorating 10 years of the Nexa brand with the launch of the Grand Vitara Phantom Blaq Edition. The vehicle is finished in an exclusive Matte Black colour.
The Grand Vitara Phantom Blaq Edition is available in the Strong Hybrid Alpha+ variant, which features matte black finish on the exterior and all-black with perforated faux leather upholstery and champagne gold accents on the interior.
Partho Banerjee, Senior Executive Officer, Marketing & Sales, Maruti Suzuki India, said, “As we celebrate a decade of Nexa, the Grand Vitara Phantom Blaq Edition reflects our ongoing commitment to inspire customers with specially curated innovations. This Limited Edition captures the essence of indulgence, offering an SUV that not only performs exceptionally but also aligns perfectly with the refined lifestyles of our discerning buyers. Since its debut, the Grand Vitara has garnered an exceptional response, achieving the milestone of 300,000 sales in just 32 months, setting a new benchmark in the mid-size SUV segment in India. This success is driven by its versatile powertrain portfolio, offering customers the choice of Strong Hybrid, Allgrip Select, and S-CNG powertrain options, catering to diverse customer needs. The exclusive new Grand Vitara Phantom Blaq is set to elevate its desirability further.”
The Grand Vitara Phantom Blaq Edition has a panoramic sunroof and ventilated front seats with perforated faux leather. It features a 22.86cm (9-inch) SmartPlay Pro+ infotainment system with wireless Android Auto and Apple CarPlay, as well as a Clarion sound system. A 360-degree camera, Head-Up Display and wireless charging dock are also included. The vehicle uses Suzuki Connect for car capabilities.
Safety features on the Grand Vitara include 6 airbags, Electronic Stability Program (ESP), Anti-lock Braking System (ABS) with Electronic Brakeforce Distribution (EBD), Hill Hold Control, and reverse parking sensors.
- Citroen India
- Stellantis
- Shailesh Hazela
- MS Dhona
- C3
- Aircross
- Basalt Coupe
- Shift Into The New
- Citroen 2.0
Citroen India Unveils Citroen 2.0 Shift Into the New Strategic Plan
- By MT Bureau
- August 08, 2025
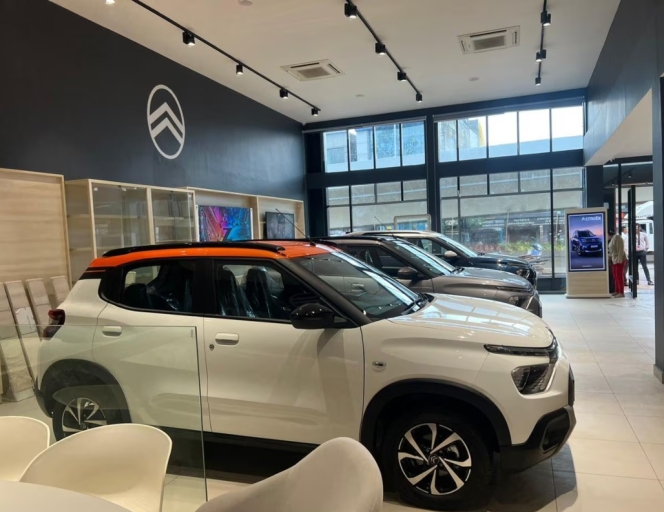
Stellantis-owned Citroen India has announced the launch of its ‘Citroen 2.0 – Shift Into the New’ strategy, aimed at strengthening its position as an accessible mobility brand in the country. The plan focuses on enhanced customer satisfaction, product innovation and a significant expansion of its network across India.
The initiative includes upgrades to the C3, Aircross and Basalt Coupe SUV, with improvements in design, in-cabin technology and comfort. Developed on the global C-Cubed platform with up to 98 percent localisation, the refreshed portfolio is tailored to Indian driving conditions.
Shailesh Hazela, CEO & MD, Stellantis India, said, “India represents one of the most exciting and demanding opportunities for Stellantis globally and our Citroen 2.0 – Shift Into the New strategic plan is a decisive step forward in our commitment to India. We’re aligning closer than ever with Indian customers through locally engineered products, deeper network reach, and a relentless focus on quality and customer centricity. This is not about quick wins – it’s about sustainable growth, built on trust and long-term value. With high localisation, strong after-sales systems, newer ways of customer engagement and a sharp understanding of evolving expectations, we’re here to grow with India and for India.”
Since entering the market in 2021 with 10 showrooms, Citroen has grown to over 80 customer touchpoints, with plans to double the number by the end of this year. The expansion will prioritise Tier II, III and IV markets, supported by a digital service model offering transparent pricing and real-time tracking.
The company has invested over INR 53 billion in manufacturing, product platforms and localisation, with further investments planned in EVs, ICE platforms and supply chain localisation. The strategic plan will be introduced with a teaser featuring cricket legend MS Dhoni as brand ambassador.
Hyundai, General Motors Join Forces To Develop 5 New Vehicles
- By MT Bureau
- August 08, 2025
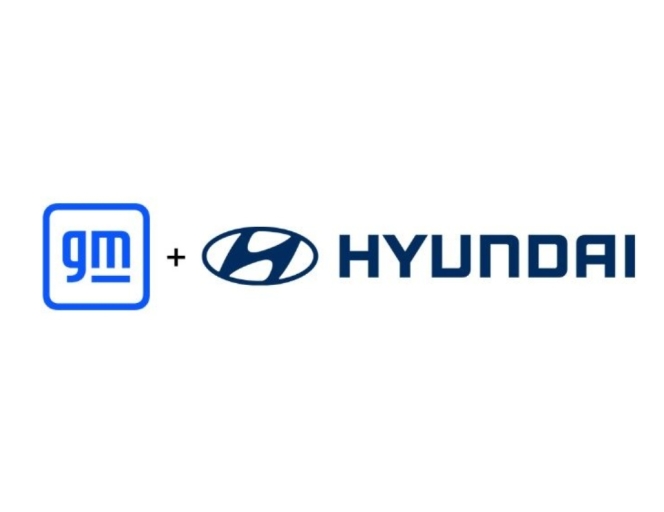
South Korean auto major Hyundai Motor Company and American automaker General Motors have joined forces to develop five new vehicles, including four for Central and South America and one for the North American market. The partnership aims to leverage the companies' combined scale to bring new models to customers faster and at a lower cost.
The collaboration will produce a compact SUV, car, and two different pickup trucks for Central and South American markets. These vehicles will be flexible, offering both traditional internal combustion engines and hybrid options. For North America, the companies will co-develop an electric commercial van.
The new vehicles are slated to launch starting in 2028. GM will take the lead on developing the mid-size truck platform, while Hyundai will spearhead the compact vehicle and electric van projects. While the vehicles will share platforms, each company will design unique interiors and exteriors to reflect its own brand.
This strategic collaboration is expected to produce more than 800,000 vehicles annually once production is fully scaled. The companies also plan to explore joint sourcing for materials and logistics, and are committed to sustainable manufacturing, including the use of low-carbon emissions steel.
Jose Munoz, President and CEO, Hyundai Motor Company, said, “Hyundai’s strategic collaboration with GM will help us continue to deliver value and choice to our customers across multiple vehicle segments and markets. Our combined scale in North and South America helps us to more efficiently provide our customers more of what they want – beautifully designed, high-quality, safety focused vehicles with technology they appreciate.”
Shilpan Amin, GM's Senior Vice-President and Global Chief Procurement and Supply Chain Officer, said, “By partnering together, GM and Hyundai will bring more choice to our customers faster, and at lower cost. These first co-developed vehicles clearly demonstrate how GM and Hyundai will leverage our complementary strengths and combined scale.”
The partnership, which was announced in September 2024, is still exploring other potential joint ventures, including collaboration on additional vehicle programs and propulsion systems like hydrogen fuel cell technology.
CUPRA Launches Shadow Edition Leon Models
- By MT Bureau
- August 07, 2025
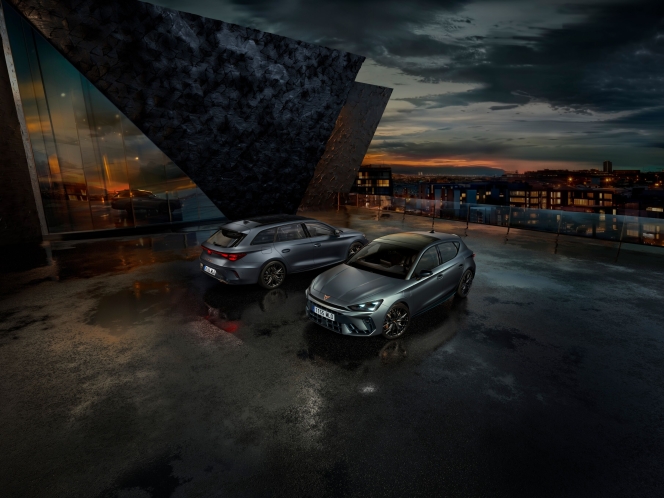
CUPRA has introduced new Shadow Edition variants for its Leon and Leon Estate models in the UK, featuring bold dark styling accents that amplify the brand's sporty aesthetic. Based on the V3 trim, these editions come equipped with premium features such as leather upholstery, advanced driver aids and Dynamic Chassis Control.
The exterior showcases 19-inch matte black alloy wheels, black side skirts and a sleek roof spoiler, complemented by advanced CUPRA Matrix LED ULTRA headlights for superior nighttime visibility. Buyers can opt for the IMMERSIVE by Sennheiser sound system, which includes a 10-speaker setup with a subwoofer for an enhanced audio experience.
Additional upgrades like a panoramic sunroof, towbar, and various paint options are also available. Starting at GBP 36,770, the Shadow Edition is now open for orders in the UK.
Marcus Gossen, Managing Director of SEAT and CUPRA UK, said, “The launch of the Shadow Edition in the UK is a big step forward in the design journey of the CUPRA Leon. The Leon is the flagship hatchback of the brand and remains a disruptor and a style-leading icon in the market. The new features of the Shadow Edition combine striking design and leading technology to ensure that the Leon continues to be a popular choice for drivers.”
Comments (0)
ADD COMMENT