Aluminium Can Play A Pivotal Role In The Changing Face Of The Automotive Sector
- By MT Bureau
- October 13, 2020
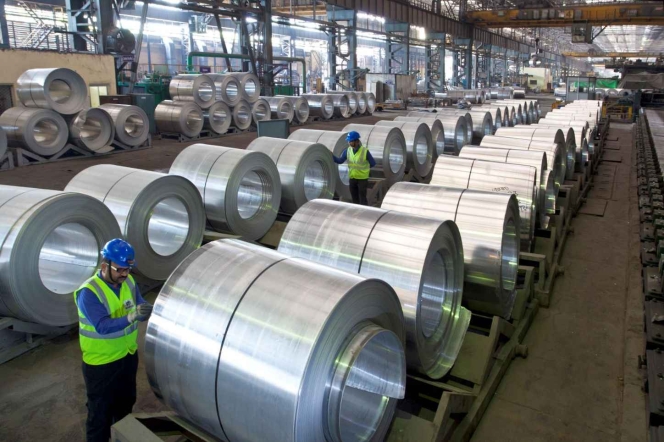

Currently, India’s foundry market for automotive components is small (only 10 percent of total foundry market — 10 million of cast iron + aluminium) in comparison to USA’s foundry market, which is at 14 million tonnes per annum, of which 3.3 million is aluminium (24 percent). With an increasing focus on higher performance with better safety and lower emission, this gap is going to shrink in the coming years, anticipates Ajay Kapur, CEO – Aluminium & Power Business, Vedanta Aluminium.
“There is immense scope for Indian aluminium producers to tap into the emerging market in the automotive sector,” said Kapur. Vedanta Aluminium was the first in India to supply PFA (primary foundry alloy) to the domestic auto sector. Before, the launch of PFA by the company, India’s entire PFA demand was being met through imports, even though the country has the world’s second-largest aluminium production capacity. Looking at the potential of the auto market and its import dependency, the company decided to tap into the opportunity and develop indigenous capabilities at its state-of-the-art facilities in Jharsuguda and BALCO to meet that demand. Currently, the company has a PFA casting capacity of 240KT spread across its plants in Odisha and Chhattisgarh.
“Primary aluminium producers develop PFAs which are customised to suit the exact needs of automakers in terms of performance, strength, durability, etc. Significant R&D and technical expertise go into developing PFAs, resulting in excellent metal quality and outstanding castability, which makes these alloys the preferred choice for the automotive industry,” explained Kapur. PFAs are ideal for aluminium alloy wheels, cylinder heads and brakes. The company also anticipates that with an increased focus on reduction of vehicle weight with higher safety performance, automotive parts critical to safety will be made from PFA instead of cast iron to offer higher strength and nearly double absorption of crash energy. “Besides, aluminium PFAs will always have the added advantage of cost-saving on fuel and maintenance,” added Kapur.
Vedanta Aluminium has started steadily supplying PFAs to OEMs and ancillaries in wheel manufacturing in India. “Our proactive move to expand business on this front helped us on-board some of the most reputed equipment manufacturers and auto ancillaries as our clients, and we have received a very positive response from them. Encouraged by that, we will soon look to expand our alloy portfolio for supporting manufacturing of cylinder heads, ABS brakes and certain key applications where traditional materials can easily get substituted with aluminium alloy. We are also exploring prospects of long-term investments by auto ancillaries near our aluminium smelters so that they may leverage cost savings in terms of freight, re-melting and electricity,” said Kapur.
The company, according to him, is well-positioned to cater to the current and emerging needs of the Indian auto sector, offering a broad range of products that find usage across the automotive value chain – from casting to extrusion. “When choosing suppliers for alloys, automotive players should look for companies having high-quality casting facilities, sophisticated R&D facilities and technological prowess for developing customised high-performance alloys for their specific needs, and finally, having robust after-sales technical support; USPs that have earned us the trust of our clients,” he added.
Aluminium is the second most used metal in the world after steel, today, and, according to Kapur, it has the potential to become the most important commercial metal in the future. “Most developed countries have already designated aluminium as a core industry. Aluminium holds strategic importance for the economy as the metal of choice for all kinds of transportation, power, aerospace, defence, building and construction needs. So, given the role it plays in supporting the core sectors meet the Government’s ‘Make in India’ initiative, we expect its application to only expand with time,” said Kapur.
The metal’s usage in the transportation sector has been rapidly increasing as it offers an environment-friendly and cost-effective way to increase performance, boost fuel economy and reduce emissions while maintaining or improving safety and durability. Aluminium is substantially lighter than its counterparts, offering a significant reduction in weight, which has a direct impact on fuel consumption and carbon emissions.
The metal also has a higher strength-to-weight ratio compared to traditional materials that enable it to absorb twice the crash energy of mild steel, ensuring that vehicular performance enhancements do not come at the cost of safety. “Further, nearly 90 percent of all the aluminium used in a vehicle is recycled at the end of its lifecycle. The energy required to recycle aluminium is only five percent of the energy required to produce the metal. With all these advantages, aluminium can play a pivotal role in the changing face of the automotive sector,” said Kapur.
Aluminium alloys are used by the Indian auto industry majorly as alloy wheels. Around 95 percent of two-wheelers include aluminium, averaging at 7kg per bike, taking total consumption of aluminium alloy in this segment to 115KTPA (kilo tons per annum). Whereas, only 20 percent of four-wheelers use aluminium, majorly in high-end models, which max out at 40kg per car. “The crux of the matter is, in India, we are yet to explore more applications of aluminium in the automotive industry akin to our global peers. For example, in developed countries, around 21 PFAs are used in the automotive segment to achieve light-weighting in the form of various auto parts and components. In India, we majorly use PFAs only for manufacturing alloy wheels and to some extent, for cylinder heads. So, there is immense potential for usage of aluminium in other auto parts like engine, suspension, front end carrier, instrument panel support, rear frame, chassis and many more,” said Kapur.
Shortly, the company expands its alloy portfolio for supporting manufacturing of cylinder heads, ABS brakes and certain other applications where currently steel or iron is being used but can be substituted by suitable aluminium alloys to provide additional benefits. As the market for aluminium alloys in automotive segment expands with inclusion of newer applications, Vedanta Aluminium will look for opportunities to leverage its technological expertise and R&D capabilities to develop products customised to the needs of the market. Vedanta Aluminium is also open to collaborating with the downstream industry, to unlock the entire potential of aluminium used in the auto sector and cater to the rapidly evolving aluminium requirements of the Indian automotive industry.
In the Indian automotive market, one of the biggest challenges faced today is the increasing imports of auto components from China and other countries. The size of the auto components imports was USD 17.6 billion in FY19. Asia, the largest source of imports for Indian auto-components, had a share of 61 percent followed by Europe at 29 percent; North America at eight percent; Latin America and Africa at one percent each in FY19. China, with 27 percent, enjoyed the status of the largest exporter in the Indian automotive market.
“The potential of the aluminium industry should be acknowledged and recognised as a core sector with a National Aluminium Policy that will encourage, protect and boost the domestic aluminium industry. The domestic capability needs to be harnessed for critical sectors of national importance like defence, aerospace, aviation, transportation, infrastructure, electrification, housing, etc. We must make the vision of ‘Make in India’ a ground reality in these sectors, leveraging the potential of the entire aluminium value chain, from mining to end usage. Besides enhancing domestic capacity and reducing import dependency and subsequently trade deficit, it will also generate huge employment opportunities in our country which has a deep talent pool that needs to be capitalised for the realisation of our vision of a USD5 trillion economy. We are on the right path, but there is still a long way to go,” said Kapur.
The global economy is swiftly moving towards a cleaner, greener and more sustainable lifestyle. For more than a decade now, concerns about fuel efficiency have encouraged OEMs to replace steel with aluminium in vehicle bodies, doors, trunks, hoods, bumpers, crash boxes, brakes and wheels. With the advent of electric vehicles (EV), OEMs worldwide are focusing on exploring and applying new uses of aluminium. The need for lightweight battery casings and heat exchangers in electric vehicles, combined with autonomous vehicles’ demands for high visibility and structural integrity, is expected to exponentially increase the use of aluminium in cars, trucks and buses from now on. “Using aluminium in EVs has several advantages, foremost amongst which is the distance travelled per charge. Lighter the vehicle, the longer its range. Coming to better battery life, thanks to the metal’s thermal and anticorrosion properties, aluminium is ideal for battery frames. Demand for aluminium will also rise on account of infrastructure for serving EVs since the metal is commonly used as a housing material for EVs charging stations as well. While India is waking up to this future of automobiles, partnerships between different automotive industry bodies/institutions and auto companies for sharing knowledge and expertise will help fast-track development of electric vehicles in the country,” said Kapur. MT
- Automotive Research Association of India
- ARAI
- ADAS
- ADAS Test City
- ADAS Show
- Dr. Reji Mathai
- Syed Fareed Ahmed
ARAI Gears Up To Host The ADAS Show In December 2025 At New ADAS Test Facility In Pune
- By MT Bureau
- September 03, 2025
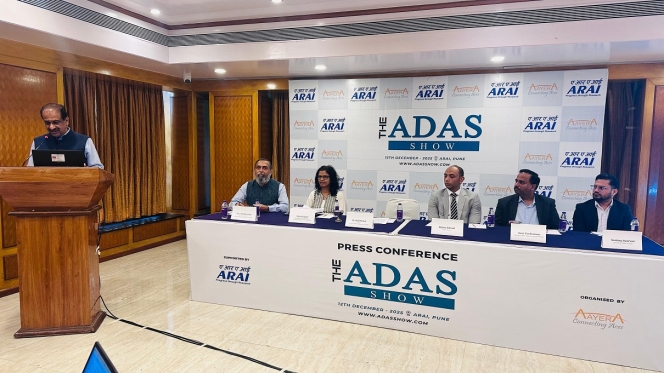
The Automotive Research Association of India (ARAI), an autonomous body under the Ministry of Heavy Industries, Government of India, has announced the readiness of its ambitious and pioneering project, the ‘ADAS Test City’.
The new facility spread across 20 acres in Takwe near Talegaon, Pune, is designed as a pseudo city to replicate the diverse road conditions in India, which will be instrumental to test and validate Advanced Driver Assistance Systems (ADAS) in a safe, secure, repeatable and controlled environment. The idea is to support the development of ADAS solutions to meet the real-world scenarios in India. The ADAS Test City is also the first-of-its-kind such dedicated facility in the country.
Furthermore, ARAI also announced that it will host ‘The ADAS Show’ in association with Aayera, at the new facility on 12 December 2025, where it expects automakers, tier 1 suppliers and technology companies to showcase their innovation and test vehicles.
Dr. Reji Mathai, Director, ARAI said, “ADAS are pivotal in enhancing road safety, and ARAI remains committed to driving the adoption of safe, smart, and sustainable mobility solutions across industry. Our upcoming ADAS Smart City Track represents a landmark initiative – India’s first dedicated proving ground designed to enable automotive and auto-tech manufacturers to rigorously test and validate their technologies in real-world conditions. We thank the Ministry of Heavy Industries for their gracious support under their Capital Goods Scheme which has enabled us to install the modular infrastructure for Verification and Validation of ADAS at the Test City. This facility will play a crucial role in advancing ADAS capabilities by empowering manufacturers to deliver best-in-class safety solutions to consumers. Moreover, this ADAS Smart City Track will not only facilitate but will boost indigenous ADAS/AV technology development from the budding start-up ecosystem. Hence, events such as The Adas Show, organised in collaboration with Aayera, are instrumental in fostering open dialogue and collaborative innovation in the realm of intelligent mobility. We look forward to insightful deliberations and a successful event on 12th December 2025.”
Syed Fareed Ahmed, Director, Aayera, added, “THE ADAS SHOW is India’s definitive platform where automotive leaders, technologists, and innovators converge to showcase and discuss the most advanced driver-assistance and safety technologies. The previous editions were inaugurated by Dr. Hanif Qureshi, IPS, Additional Secretary (Automobiles), Ministry of Heavy Industries, Government of India at ICAT, and witnessed participation from leading OEMs such as Honda, JSW MG Motors, BMW, Volvo, Mahindra & Mahindra, Tata Motors, Maruti Suzuki India, alongside global technology leaders including Bosch, ZF, Valeo, Harman, Starkenn, Rosmerta, Dassault Systemes, NXP, Uno Minda and many more. The Adas Show is a dynamic and engaging event that unites vehicle manufacturers, ADAS technology companies and testing equipment providers to present cutting-edge innovations in real-world scenarios.”
LTTS Partners SiMa.ai To Drive Innovation Across Mobility, Industrial Automation & Robotics
- By MT Bureau
- September 03, 2025
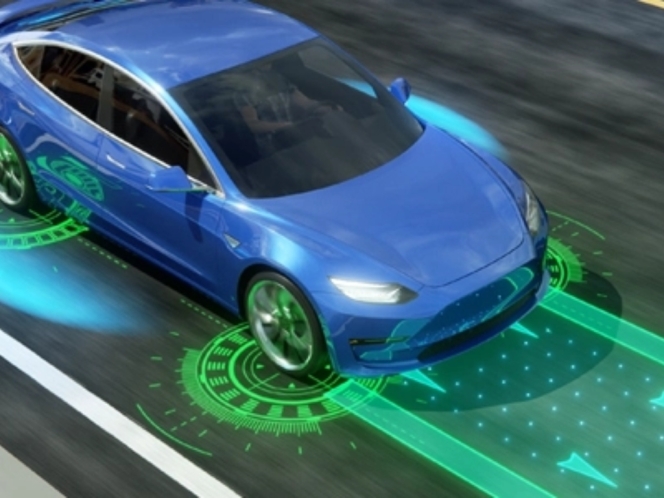
Bengaluru-headquartered engineering R&D service company L&T Technology Services has inked a strategic partnership with Silicon Valley-based SiMa.ai, a leader in Physical AI. The partnership will focus on driving AI-driven solutions across mobility, healthcare, industrial automation and robotics.
As per the understanding, LTTS’ will combine its deep engineering expertise and domain focus with SiMa.ai’s MLSoC ONE platform and software SDK. SiMa.ai will deliver industry-leading AI hardware and software solutions by leveraging LTTS’ core engineering capabilities and human capital investments across key areas such as in-vehicle infotainment (IVI), AD/ADAS, industrial automation & robotics and healthcare.
Amit Chadha, CEO & MD, L&T Technology Services, said, “SiMa.ai cements LTTS’ position as a leader in AI-led ER&D solutions. By combining SiMa.ai’s groundbreaking AI computing technology with our expertise in design and implementation, we are empowering clients across robotics, mobility and healthcare to accelerate time-to-market, enhance operational efficiency and deliver unparalleled value. Together, we are driving the industry forward, embedding intelligence into innovative solutions that are sustainable and scalable.”
Krishna Rangasayee, Founder & CEO, SiMa.ai, said, “Our collaboration with LTTS symbolises the synergy required to scale physical AI applications globally. LTTS brings unmatched engineering capabilities and client reach, making them an ideal partner. By working together, we enable industries to harness the full potential of AI, delivering high performance and power efficiency to clients while simplifying the adoption process.”
Rapido And Jaipur Police Partner To Enhance Women's Safety In City's Cabs
- By MT Bureau
- September 02, 2025
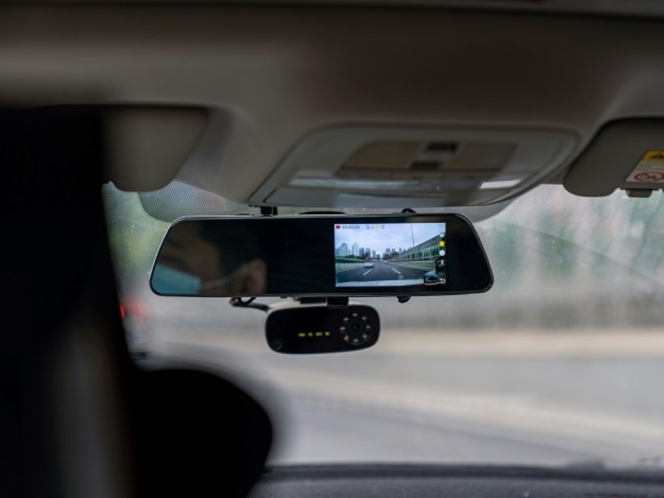
Rapido, a leading ride-sharing platform in India, has joined forces with the Jaipur Police Commissionerate to launch a new initiative focused on improving women's safety in the city's public transportation. This partnership, which follows a week-long awareness campaign, will see the installation of dashcams in 100 Rapido cabs to enhance ride monitoring and emergency response times.
Rapido stated that at present, 40 percent of its cab users in Jaipur are women. The initiative, titled ‘Sashakt Nari – Zimmedari Hamari’ (Empowered Women – Our Responsibility), was flagged off by Jaipur Police Commissioner Biju George Joseph and Deputy Commissioner of Police Rajarshi Raj. The campaign underscores the shared responsibility of citizens, service providers and law enforcement in ensuring women can travel safely and with confidence.
Rajarshi Raji said, "Women's safety is a collective responsibility that goes beyond the role of the police. When communities, technology partners, and law enforcement work together, we can create a safer and more supportive environment for women. Initiatives like this campaign help build confidence, enabling women to move freely for work, education and daily life."
Sudipta Sen, Senior Manager at Rapido Cabs, noted, "At Rapido, safety is not an add-on; it is the foundation of every ride. With 40% of cab users in Jaipur being women, our collaboration with Jaipur Police focuses on practical measures that can make every journey safer and more reassuring. By introducing dashcams, providing 24x7 support, and driving awareness campaigns, we are working to make mobility safer, inclusive and truly empowering for women. Our goal is to ensure that every woman in Jaipur should be able to travel with confidence and see mobility as a catalyst for her independence and participation in the city’s growth.”
The dashcams will supplement Rapido's existing safety features, which include an in-app SOS button, real-time ride tracking and a call-masking feature for female customers.
OrbitsIQ Global Acquires UNIO Enterprise In Landmark Deal To Revolutionise Mobile Connectivity
- By MT Bureau
- September 02, 2025
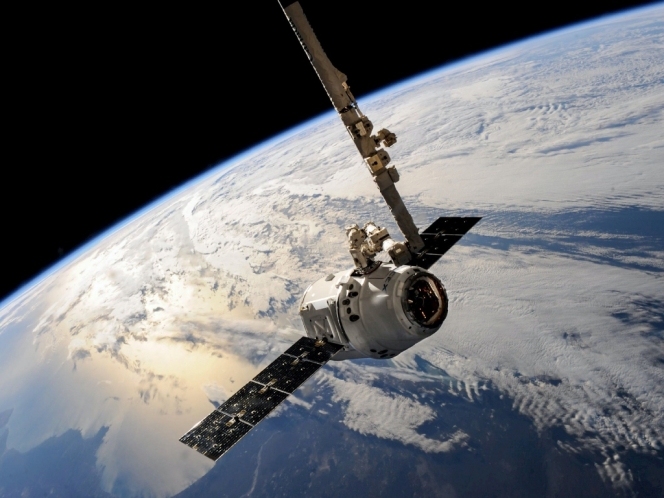
In a major move set to redefine global connectivity for mobile assets, Luxembourg-based OrbitsIQ Global (OIQ) has completed the acquisition of Munich-based NewSpace startup, UNIO Enterprise. The deal, which combines UNIO’s pioneering connectivity software with OIQ's satellite and terrestrial network capabilities, aims to provide seamless, uninterrupted service to millions of vehicles, boats, planes and autonomous systems worldwide.
The merger is poised to create a ‘ubiquitous bridge’ between cellular and satellite networks, ensuring constant connectivity for mobile assets. The partnership is a significant step towards enabling critical technologies like autonomous driving, smart logistics and predictive maintenance, all of which rely on uninterrupted data flow.
Katrin Bacic, CEO, UNIO Enterprise, said, "Joining OIQ Global marks a turning point for UNIO. With our connectivity expertise and OIQ’s constellation vision, we will redefine how mobility assets connect. This partnership allows us to accelerate our roadmap and deliver the next generation of intelligent connectivity across terrestrial and satellite networks for industries such as automotive, agriculture, logistics and maritime sectors."
Joseph J Euteneuer, CEO, OIQ Global, said, "We are delighted to welcome UNIO Enterprise into the OIQ Global family. Their AI-powered smart-switch connectivity technology is the perfect complement to our global anywhere anytime connectivity vision. Together, we will establish a seamless, multi-band mobility connectivity capability that unlocks new frontiers in efficiency, safety and operational insight around the world."
The companies believe this acquisition positions Europe at the forefront of global telematics innovation, strengthening the continent’s leadership in a field where mobility connectivity has become as essential as fuel.
Comments (0)
ADD COMMENT