Hyundai's Manufacturing Excellence Eased Making All-new i20
- By MT Bureau
- October 27, 2020
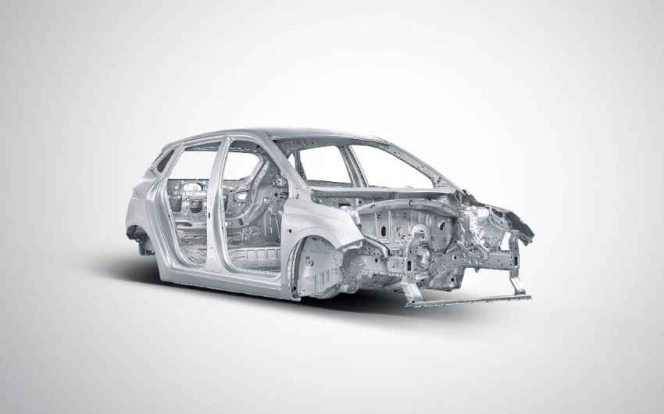

Hyundai Motor India has showcased its Manufacturing Excellence through the origins of the all-new i20, a Masterpiece of Human Centric Engineering. With unassailable standards and processes, the company has created the all-new i20 that is perfected through a prudent use of Industry 4.0 and Automation.
Ganesh Mani S, Director – Production, Hyundai Motor India, said, “Our focus has remained on ensuring supreme levels of manufacturing excellence. This has perfectly culminated in the all-new i20, delivering robust and reliable performance. With our 24-year rich manufacturing heritage of ‘Make in India’, the all-new i20 is yet another benchmark brand from Hyundai that is an edge above the rest.”
THE ROBUST SUPERSTRUCTURE:
- Featuring an extensive application of 66 % Advanced & High-Strength Steel, Hyundai has created a Robust Superstructure to enhance crash worthiness and make the car lighter.
- This super structure is created, using 5,400 Tons Stamping at the Press Shop
- Incorporating an Online Condition Monitoring systems to monitor machine vibration, Hyundai offers enhanced process quality, changing shapes of metal in elegant curves & creases.
- The use of advanced Digital gauge to check the Panel thinning distribution - Crack, Neck Prediction methodology that helps in manufacturing ZERO Crack panels.
- Hyundai has used ‘High quality grade coils’ for sculpturing aesthetics and modern look of the all-new i20.
- Use of 3D scanning of Parts – to analyse and strengthen the press panel parts accuracy and precision
THE IMPECCABLE APPEAL:
- The all-new i20’s dynamic and futuristic appeal is created at the Body Shop on the Global Body Build Line.
- Using technology enabled high-quality welding process that features over 450 4th Gen Robots offering 100 % Weld Automation with over 4,000 welding spots in each car, and more than 70 cars being processed every hour
- Robots on the Line offer a glimpse of the flawless manufacturing process that gives a definitive shape to the origins of the all-new i20.
- Body shop has three stage advance quality conformation where our quality system is enable with ‘Quality 4.0 techniques’
- Intelligent weld monitoring
- Real time weld quality confirmation system [Colour tip sensor]
- Real time sealer quality confirmation system
- In house Data scientists in shop floor apply Deep learning techniques for Quality confirmation of Mastic Sealer through Vision Inspection system
THE VIBRANT CHARISMA:
- Vivid and striking colours of the all-new i20 are curated at the Paint Shop where High Throw Power 7th Generation Electro Deposition Paint is applied for long lasting Rust Warranty and corrosion resistance.
- The vibrant charisma of the all-new i20 is processed in seamless automation line that features 72 Robots ensuring the conformity to supreme quality standards and long lasting stylish & glossy looks.
- Using an Anode Cell Current Monitoring system, Hyundai has enhanced the paint application quality through an Online Current monitoring method.
THE DYNAMIC PERFORMANCE:
- Through immense research, hours of design, validation and testing of multiple iterations of operating condition, the all-new i20 has been prepared to offer rip-roaring performance.
- To give these engines robust performance, Hyundai has employed technologically superior treatment that enhances its performance on road.
- The in-house Endurance lab tests the performance with load condition for 849 Hours and without load condition for 5 lakhs cycles for transmission systems, and over 350 hours for the Engine system, to ensure enhanced durability
- Hyundai also employs a Cold Test Bed that is an eco-friendly way of testing the engines over 15 parameters, without burning fuel. It is a fully automated system in which 100% of the produced engines are tested before assembling in vehicles.
- At the Powertrain Shop, Hyundai manufactures both diesel & petrol engines using 700 CNC Machines with Integrated SPC (Statistical Process Control).
- With High Speed Vision (60 frames/ minute) 58 Engine parts are verified, offering robust Quality for a Pleasurable Driving Experience.
THE PARADIGM OF QUALITY:
- To drive enhanced convenience and confidence, Hyundai’s assembly lines are ready to convert robust shells into fully functioning cars in the Assembly Shop.
- Here 80% of the car’s parts are fixed, preparing it through a 100% systemized 3 stage dynamic tightening confirmation that features:
- Electric tool tightening 700+ dynamic joints per car (safety and critical parts)
- Re-confirmation system across all the line (Trim, Chassis and Final line)
- Tightening quality and Sign-off interlock to ensure zero defect vehicle rollout
- Additionally, systemized part feeding method is used for maintaining quality in feeding and assembly operation using:
- Global Part Traceability Information System
- Advanced Part Management System
- Mobility Sequence Feeding System
- Trolley Scheduling System
- Through a 324-point check in HIDIS (Hyundai Integrated Digital Inspection System), Hyundai is ensuring the highest levels of conformation to quality standards.
- Each and every vehicle that rolls of the assembly line - right from the stage of panel press to complete vehicle roll out is thoroughly inspected by over 500 quality in-charge experts.
- Vehicle final inspection method is digitally enabled for assembled part specification/ type verification.
- The all-new i20 then undergoes a dynamic road test on 18 drive tracks for various road driving conditions as well as a unique leak test that is equivalent to driving through rain/water pressure that exceeds the heaviest recorded monsoons, with a shower condition of 60mm per minute or 3,600mm per hour at a pressure of 3bar.
The all-new i20 has been developed to create a Masterpiece of Human Centric Engineering that encompasses Human, Machine and Emotions, offering Quality Time to its Valued Customers.
- Automotive Research Association of India
- ARAI
- ADAS
- ADAS Test City
- ADAS Show
- Dr. Reji Mathai
- Syed Fareed Ahmed
ARAI Gears Up To Host The ADAS Show In December 2025 At New ADAS Test Facility In Pune
- By MT Bureau
- September 03, 2025
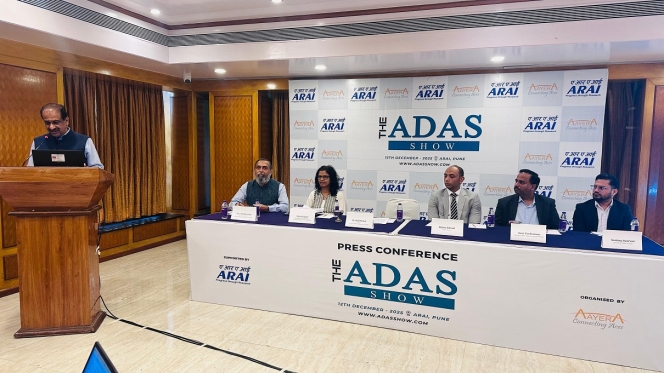
The Automotive Research Association of India (ARAI), an autonomous body under the Ministry of Heavy Industries, Government of India, has announced the readiness of its ambitious and pioneering project, the ‘ADAS Test City’.
The new facility spread across 20 acres in Takwe near Talegaon, Pune, is designed as a pseudo city to replicate the diverse road conditions in India, which will be instrumental to test and validate Advanced Driver Assistance Systems (ADAS) in a safe, secure, repeatable and controlled environment. The idea is to support the development of ADAS solutions to meet the real-world scenarios in India. The ADAS Test City is also the first-of-its-kind such dedicated facility in the country.
Furthermore, ARAI also announced that it will host ‘The ADAS Show’ in association with Aayera, at the new facility on 12 December 2025, where it expects automakers, tier 1 suppliers and technology companies to showcase their innovation and test vehicles.
Dr. Reji Mathai, Director, ARAI said, “ADAS are pivotal in enhancing road safety, and ARAI remains committed to driving the adoption of safe, smart, and sustainable mobility solutions across industry. Our upcoming ADAS Smart City Track represents a landmark initiative – India’s first dedicated proving ground designed to enable automotive and auto-tech manufacturers to rigorously test and validate their technologies in real-world conditions. We thank the Ministry of Heavy Industries for their gracious support under their Capital Goods Scheme which has enabled us to install the modular infrastructure for Verification and Validation of ADAS at the Test City. This facility will play a crucial role in advancing ADAS capabilities by empowering manufacturers to deliver best-in-class safety solutions to consumers. Moreover, this ADAS Smart City Track will not only facilitate but will boost indigenous ADAS/AV technology development from the budding start-up ecosystem. Hence, events such as The Adas Show, organised in collaboration with Aayera, are instrumental in fostering open dialogue and collaborative innovation in the realm of intelligent mobility. We look forward to insightful deliberations and a successful event on 12th December 2025.”
Syed Fareed Ahmed, Director, Aayera, added, “THE ADAS SHOW is India’s definitive platform where automotive leaders, technologists, and innovators converge to showcase and discuss the most advanced driver-assistance and safety technologies. The previous editions were inaugurated by Dr. Hanif Qureshi, IPS, Additional Secretary (Automobiles), Ministry of Heavy Industries, Government of India at ICAT, and witnessed participation from leading OEMs such as Honda, JSW MG Motors, BMW, Volvo, Mahindra & Mahindra, Tata Motors, Maruti Suzuki India, alongside global technology leaders including Bosch, ZF, Valeo, Harman, Starkenn, Rosmerta, Dassault Systemes, NXP, Uno Minda and many more. The Adas Show is a dynamic and engaging event that unites vehicle manufacturers, ADAS technology companies and testing equipment providers to present cutting-edge innovations in real-world scenarios.”
LTTS Partners SiMa.ai To Drive Innovation Across Mobility, Industrial Automation & Robotics
- By MT Bureau
- September 03, 2025
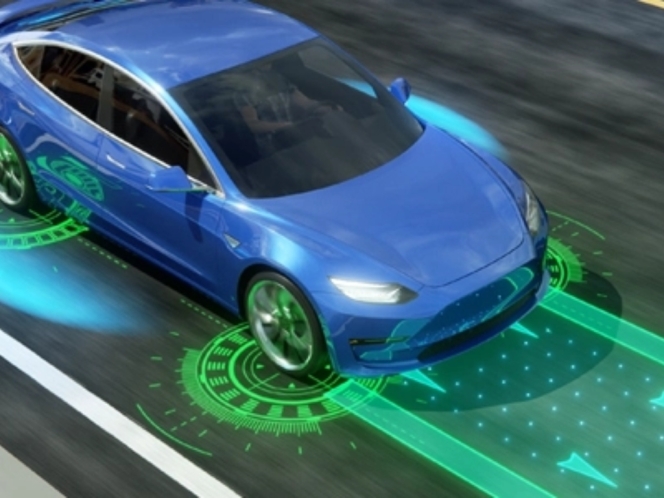
Bengaluru-headquartered engineering R&D service company L&T Technology Services has inked a strategic partnership with Silicon Valley-based SiMa.ai, a leader in Physical AI. The partnership will focus on driving AI-driven solutions across mobility, healthcare, industrial automation and robotics.
As per the understanding, LTTS’ will combine its deep engineering expertise and domain focus with SiMa.ai’s MLSoC ONE platform and software SDK. SiMa.ai will deliver industry-leading AI hardware and software solutions by leveraging LTTS’ core engineering capabilities and human capital investments across key areas such as in-vehicle infotainment (IVI), AD/ADAS, industrial automation & robotics and healthcare.
Amit Chadha, CEO & MD, L&T Technology Services, said, “SiMa.ai cements LTTS’ position as a leader in AI-led ER&D solutions. By combining SiMa.ai’s groundbreaking AI computing technology with our expertise in design and implementation, we are empowering clients across robotics, mobility and healthcare to accelerate time-to-market, enhance operational efficiency and deliver unparalleled value. Together, we are driving the industry forward, embedding intelligence into innovative solutions that are sustainable and scalable.”
Krishna Rangasayee, Founder & CEO, SiMa.ai, said, “Our collaboration with LTTS symbolises the synergy required to scale physical AI applications globally. LTTS brings unmatched engineering capabilities and client reach, making them an ideal partner. By working together, we enable industries to harness the full potential of AI, delivering high performance and power efficiency to clients while simplifying the adoption process.”
Rapido And Jaipur Police Partner To Enhance Women's Safety In City's Cabs
- By MT Bureau
- September 02, 2025
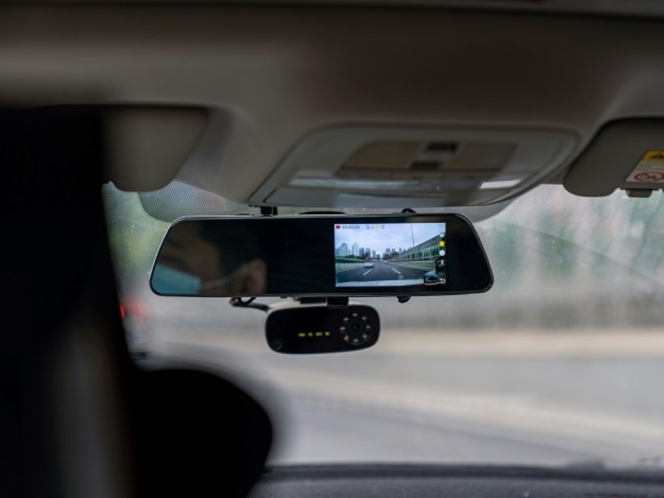
Rapido, a leading ride-sharing platform in India, has joined forces with the Jaipur Police Commissionerate to launch a new initiative focused on improving women's safety in the city's public transportation. This partnership, which follows a week-long awareness campaign, will see the installation of dashcams in 100 Rapido cabs to enhance ride monitoring and emergency response times.
Rapido stated that at present, 40 percent of its cab users in Jaipur are women. The initiative, titled ‘Sashakt Nari – Zimmedari Hamari’ (Empowered Women – Our Responsibility), was flagged off by Jaipur Police Commissioner Biju George Joseph and Deputy Commissioner of Police Rajarshi Raj. The campaign underscores the shared responsibility of citizens, service providers and law enforcement in ensuring women can travel safely and with confidence.
Rajarshi Raji said, "Women's safety is a collective responsibility that goes beyond the role of the police. When communities, technology partners, and law enforcement work together, we can create a safer and more supportive environment for women. Initiatives like this campaign help build confidence, enabling women to move freely for work, education and daily life."
Sudipta Sen, Senior Manager at Rapido Cabs, noted, "At Rapido, safety is not an add-on; it is the foundation of every ride. With 40% of cab users in Jaipur being women, our collaboration with Jaipur Police focuses on practical measures that can make every journey safer and more reassuring. By introducing dashcams, providing 24x7 support, and driving awareness campaigns, we are working to make mobility safer, inclusive and truly empowering for women. Our goal is to ensure that every woman in Jaipur should be able to travel with confidence and see mobility as a catalyst for her independence and participation in the city’s growth.”
The dashcams will supplement Rapido's existing safety features, which include an in-app SOS button, real-time ride tracking and a call-masking feature for female customers.
OrbitsIQ Global Acquires UNIO Enterprise In Landmark Deal To Revolutionise Mobile Connectivity
- By MT Bureau
- September 02, 2025
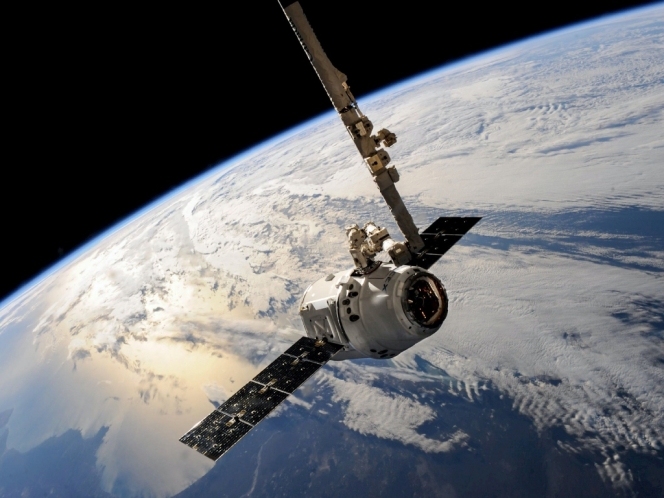
In a major move set to redefine global connectivity for mobile assets, Luxembourg-based OrbitsIQ Global (OIQ) has completed the acquisition of Munich-based NewSpace startup, UNIO Enterprise. The deal, which combines UNIO’s pioneering connectivity software with OIQ's satellite and terrestrial network capabilities, aims to provide seamless, uninterrupted service to millions of vehicles, boats, planes and autonomous systems worldwide.
The merger is poised to create a ‘ubiquitous bridge’ between cellular and satellite networks, ensuring constant connectivity for mobile assets. The partnership is a significant step towards enabling critical technologies like autonomous driving, smart logistics and predictive maintenance, all of which rely on uninterrupted data flow.
Katrin Bacic, CEO, UNIO Enterprise, said, "Joining OIQ Global marks a turning point for UNIO. With our connectivity expertise and OIQ’s constellation vision, we will redefine how mobility assets connect. This partnership allows us to accelerate our roadmap and deliver the next generation of intelligent connectivity across terrestrial and satellite networks for industries such as automotive, agriculture, logistics and maritime sectors."
Joseph J Euteneuer, CEO, OIQ Global, said, "We are delighted to welcome UNIO Enterprise into the OIQ Global family. Their AI-powered smart-switch connectivity technology is the perfect complement to our global anywhere anytime connectivity vision. Together, we will establish a seamless, multi-band mobility connectivity capability that unlocks new frontiers in efficiency, safety and operational insight around the world."
The companies believe this acquisition positions Europe at the forefront of global telematics innovation, strengthening the continent’s leadership in a field where mobility connectivity has become as essential as fuel.
Comments (0)
ADD COMMENT