- Mercedes-Benz
- electric vehicle
- battery recycling
- cobalt
- nickel
- lithium
- aluminium
- iron
- carbon black
- Jorg Burzer
- Thekla Walker MdL
- Ola Scholz
- Ola Kaellenius
Mercedes-Benz Opens Europe’s First Battery Recycling Plant In Germany
- By MT Bureau
- October 22, 2024
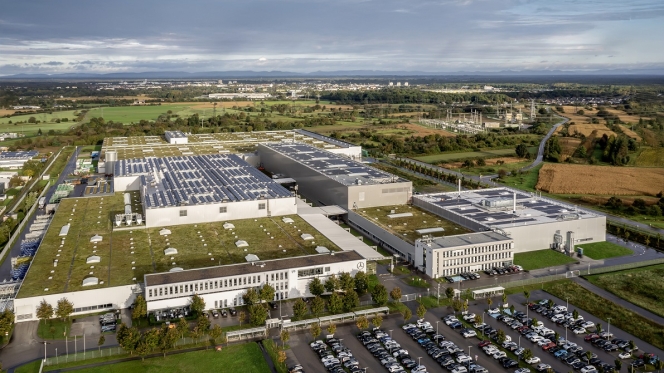
German luxury carmaker Mercedes-Benz has opened Europe's first battery recycling plant with an integrated mechanical-hydrometallurgical process making it the first car manufacturer worldwide to close the battery recycling loop with its own in-house facility.
The recycling plant in Kuppenheim, southern Germany, creates a genuine circular economy. Unlike existing established processes, the expected recovery rate of the mechanical-hydrometallurgical recycling plant is more than 96 percent. Valuable and scarce raw materials such as lithium, nickel and cobalt can be recovered – in a way which is suitable for use in new batteries for future all-electric Mercedes-Benz vehicles. The company has invested tens of millions of euros in the construction of the new battery recycling plant and thus in the value creation in Germany. Federal Chancellor Olaf Scholz and Baden-Württemberg's Environment Minister Thekla Walker visited the plant for the opening ceremony in Kuppenheim, Baden.
Ola Kaellenius, Chairman of the Board of Management, Mercedes-Benz Group said, “Mercedes-Benz has set itself the goal of building the most desirable cars in a sustainable way. As a pioneer in automotive engineering, Europe's first integrated mechanical-hydrometallurgical battery recycling factory marks a key milestone towards enhancing raw-materials sustainability. Together with our partners from industry and science, we are sending a strong signal of innovative strength for sustainable electric mobility and value creation in Germany and Europe.”
Ola Scholz said, “The future of the automobile is electric, and batteries are an essential component of this. To produce batteries in a resource-conserving and sustainable way, recycling is also key. The circular economy is a growth engine and, at the same time, an essential building block for achieving our climate targets! I congratulate Mercedes-Benz for its courage and foresight shown by this investment in Kuppenheim. Germany remains a cutting-edge market for new and innovative technologies.”
The luxury carmaker has joined hands with Primobius, a joint venture between German plant and mechanical engineering company SMS Group and Asutralian process technology developer Neometals, which is its technology partner for the battery recycling factory.
The plant is receiving funding from the German Federal Ministry for Economic Affairs and Climate Action as part of a scientific research project with three German universities. The project looks at the entire process chain for recycling, including logistics and reintegration concepts. The partners are thus making an important contribution to future scaling of the battery recycling industry in Germany.
Integrated mechanical-hydrometallurgical
For the first time in Europe, the Mercedes-Benz battery recycling plant covers all steps from shredding battery modules to drying and processing active battery materials. The mechanical process sorts and separates plastics, copper, aluminium and iron in a complex, multi-stage process. The downstream hydrometallurgical process is dedicated to the so-called black mass. These are the active materials that make up the electrodes of the battery cells. The valuable metals cobalt, nickel and lithium are extracted individually in a multi-stage chemical process. These recyclates are of battery quality and therefore suitable for use in the production of new battery cells.
Unlike the pyrometallurgy established in Europe at present, the hydrometallurgical process is less-intensive in terms of energy consumption and material waste. Its low process temperatures of up to 80deg Celsius mean it consumes less energy. In addition, like all Mercedes-Benz production plants, the recycling plant operates in a net carbon-neutral manner. It is supplied with 100 percent green electricity. The roof area of the 6800 square-metre building is equipped with a photovoltaic system with a peak output of more than 350 kilowatts.
The Mercedes-Benz battery recycling plant in Kuppenheim has an annual capacity of 2,500 tonnes. The recovered materials feed into the production of more than 50,000 battery modules for new all-electric Mercedes-Benz models. The knowledge gained could help scale up production volumes in the medium to long term.
Holistic approach
Mercedes-Benz takes a holistic approach to the circularity of battery systems and considers three core topics: circular design, value retention and closing the material loop.
With its Design for Circularity approach, the OEM is taking the entire battery technology value chain into account from the outset. At the Mercedes-Benz eCampus in Stuttgart-Unterturkheim, which opened in 2024, circular thinking flows into the development of new battery cells. Battery production for electric Mercedes-Benz vehicles is net carbon-neutral in battery factories on three continents. Local battery production is a key factor for the success of the Mercedes-Benz sustainable business strategy.
In line with circular thinking and to conserve resources, the company offers reconditioned batteries as spare parts for all its electric vehicles. In addition, its Mercedes-Benz Energy subsidiary has established a successful business model with large-scale stationary storage applications. Batteries that are no longer suitable for vehicle use can enjoy a second life as part of an energy storage system.
Jorg Burzer, Member of the Board of Management of Mercedes-Benz Group, responsible for Production, Quality & Supply Chain Management stated “We are systematically deepening our expertise in the battery value chain. Following the opening of the Mercedes-Benz eCampus for development of new battery cell chemistries in Stuttgart-Unterturkheim, we are now sustainably closing the raw materials loop in Kuppenheim. The innovative technology enables us to recover valuable raw materials from the battery with the highest possible degree of purity. This turns today's batteries into tomorrow's sustainable mine for raw materials. The new battery recycling plant strengthens the role of the Mercedes-Benz production network with vehicle and drivetrain plants in Europe.”
Thekla Walker MdL, Minister for the Environment, Climate and Energy Baden-Wurttemberg said, “Battery recycling is of great importance to Baden-Wurttemberg as a state with such a strong automotive sector. Closing the loop on the value chain reduces dependencies, increases resilience in times of crisis and can smooth peaks and troughs in the availability of raw materials. Mercedes-Benz is a pioneer in this respect: With the integrated battery recycling plant, Mercedes-Benz has developed a sustainable approach for dealing with limited resources and is therefore making a valuable contribution to a truly circular economy. We are proud that in this federal state of innovators, we are also at the forefront in this field.”
- Society of Indian Automobile Manufacturers
- SIAM
- CNG
- CBG
- LNG
- Maruti Suzuki India
- Bajaj Auto
- VE Commercial Vehicle
- NITI Aayog
- GAIL Gas
- Indrapastha Gas
- Tata Motors
SIAM, PNGRB Host Roundtable On Gas-Based Mobility For Sustainable Transport
- By MT Bureau
- July 28, 2025
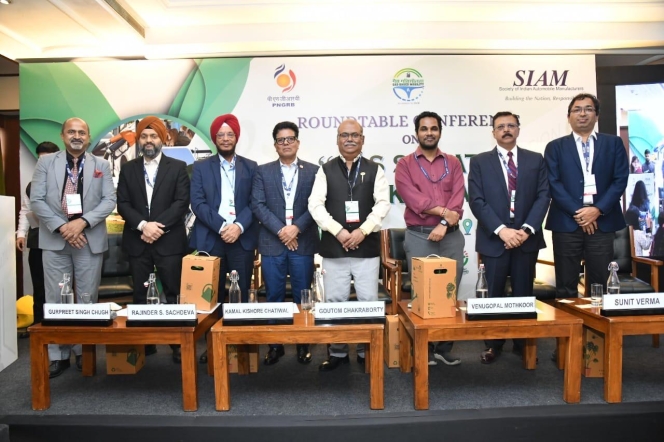
The Society of Indian Automobile Manufacturers (SIAM), in partnership with the Petroleum and Natural Gas Regulatory Board (PNGRB), convened a roundtable conference titled ‘Gas se Gati, Bharat ki Pragati’ at the India Habitat Centre, focusing on the role of gas-based fuels in promoting cleaner mobility across India.
Held under SIAM’s ‘Gas Mobility’ initiative, the event brought together government officials, industry leaders and technical experts to discuss the development of Compressed Natural Gas (CNG), Compressed Bio-Gas (CBG) and Liquefied Natural Gas (LNG) as alternative fuels for urban and long-distance transport.
In his opening address, Prashant K Banerjee, Executive Director, SIAM, said, “Globally, India is the largest user of gas fuels in mobility. We began with CNG cars and now have the largest gas-based bus and three-wheeler fleet. The launch of the world’s first CNG two-wheeler last year marked another key milestone.”
Dr Hanif Qureshi, Additional Secretary, Ministry of Heavy Industries, highlighted the role of the auto industry in achieving carbon neutrality by 2047. He noted that the government’s production-linked incentive (PLI) scheme supports gas-powered vehicles and localisation of their components.
Additional Secretary from the Ministry of New and Renewable Energy, Sudeep Jain, emphasised the potential of CBG from agricultural waste, stating that converting 10 percent of oil imports to CBG could significantly impact rural development, pollution control and energy self-sufficiency.
Maruti Suzuki’s Rahul Bharti acknowledged the government’s role in expanding CNG infrastructure, with nearly 10,000 stations targeted by 2025. He cited improvements in CNG fuel efficiency and job creation, adding that CBG and LNG also offer promising solutions for the transport sector.
The Commission for Air Quality Management’s Dr Sujit Kumar Bajpayee called gas-based transport a necessity, not a choice, especially for pollution control in Delhi-NCR. He pointed to efforts such as phasing out older vehicles and reducing stubble burning.
Dr Anil Kumar Jain, Chairperson, PNGRB, said India’s energy transition in transport is well underway and gas fuels are an effective transitional option, supported by existing infrastructure.
The thematic session, chaired by Ved Prakash Mishra of the Ministry of Environment, Forest & Climate Change, reiterated gas’s relevance until full electrification is achieved. Academic and policy experts, including IIT Kanpur’s Prof Mukesh Sharma and MNRE’s Dr Gaurav Mishra, shared data on emissions reduction and the role of bioenergy.
Presentations covered city gas expansion, vehicle technology innovations, and infrastructure challenges, featuring speakers from Bajaj Auto, Mahanagar Gas and the Association of CGD Entities.
A panel discussion on CBG and LNG adoption, moderated by ICF’s Gurpreet Singh Chugh, included input from NITI Aayog, GAIL Gas, Indraprastha Gas, VE Commercial Vehicles and Tata Motors. Speakers discussed scalability, infrastructure needs, and the role of gas in supporting India’s net-zero goals by 2070.
The event concluded with remarks by Ashish Chutani, Chairman, SIAM Gas-Based Mobility Group and Head – Government & Policy Affairs, Maruti Suzuki India.
Kinetic DX Electric Scooter Launched At INR 111,499
- By MT Bureau
- July 28, 2025
Pune-headquartered Kinetic India, a legacy name in the scooter segment, has re-entered the two-wheeler segment with the Kinetic DX EV through its EV-focused subsidiary, Kinetic Watts and Volts (KWV).
The DX range, comprising the DX and DX+, is a fully made-in-India electric scooter line designed in collaboration with Italian designers and equipped with a range of segment-first features. The e-scooters are priced at INR 111,499 for the DX and INR 117,499 for the DX+ (ex-showroom, Pune). The DX+ will be offered in Red, Blue, White, Silver, and Black, while the DX is available in Silver and Black. Bookings are open online at INR 1,000.
Both models feature a strong metal body, a spacious floorboard and the largest-in-segment 37-litre under-seat storage. They are powered by a 2.6 kWh LFP battery developed by Range-X, offering a claimed IDC range of 116 km (on the DX+). The battery promises a lifespan of over 2,500 cycles – up to four times more than standard NMC batteries – and supports a 60V system with K-Coast regenerative braking. The electric motor delivers a claimed top speed of up to 90 kmph and includes three ride modes: Range, Power and Turbo.
The DX EV range features keyless start (Easy Key), a patented retractable charging cable on the DX+ (Easy Charge), and one-touch pillion footrest deployment (Easy Flip). Both variants come with reverse and hill-hold assist, front telescopic and adjustable rear suspension, a 220mm front disc brake, and a 130mm rear drum brake with combi-braking.
The DX+ variant adds app connectivity and Telekinetic features such as real-time ride statistics, vehicle tracking, Geo-fencing and voice alerts. It also includes a Bluetooth-enabled Kinetic Assist switch, in-built speaker for music and voice navigation. Bookings are limited to 35,000 units, with deliveries starting September 2025.
Kinetic Watts & Volts has received INR 720 million in capital from Kinetic Engineering and its promoters, who have also pledged an additional INR 1.7 billion to scale the DX platform.
Ajinkya Firodia, Vice Chairman, Kinetic India, said, “The legendary Kinetic DX set so many firsts back in the ’90s, that it earned a permanent place in the hearts of millions. Reviving this icon was about more than just launching a scooter, it was about bringing back the reliability, innovation, and robustness that defined Kinetic for decades, giving it a future-ready soul. With the new DX, we’ve introduced multiple segment-first features that we’re confident, will make it a favourite in the new era of electric mobility. This marks the beginning of a bold new chapter for Kinetic and for the evolution of electric mobility in India."
Ather Energy Installs Over 400 Ather Grid Fast Charging Points In Maharashtra
- By MT Bureau
- July 24, 2025

Bengaluru-based electric two-wheeler major Ather Energy has crossed the milestone of having over 400 Ather Grid fast charging points across Maharashtra.
With 64 Experience Centres and 42 Service Centres in Maharashtra, Ather Energy has cemented its position in over 37 cities in the state. Furthermore, to provide its customers access to fast charging, it’s Ather Grid network now extends to 35 cities across Maharashtra including Mumbai, Nashik, Pune and Nagpur. It has also strategically placed the fast chargers to connect significant routes such as Mumbai - Pune, Pune - Satara, Satara - Kolhapur, Sangali - Kolhapur and Pune - Panshet.
What’s interesting to note is that customers also have access to 220 fast charging points built on the LECCS (Light Electric Combined Charging System) standard, which has been developed by Ather and opened for industry-wide adoption.
LECCS allows different brands of light electric vehicles to use the same network. Ather Grid chargers are also visible on Google Maps, making it easy for any customer with a LECCS connector on their scooter to locate, navigate and charge, further enhancing the everyday ownership experience.
Ravneet Singh Phokela, Chief Business Officer, Ather Energy, said, “Maharashtra has been a strong market for us, and we’ve seen EV adoption here grow steadily over the years. As more people switch to electric, what really builds confidence is knowing that charging won’t be a challenge. However, for many potential buyers, charging continues to be one of the perceived barriers, and that’s something we’ve always worked towards solving. From the beginning, we’ve focused on building infrastructure that keeps pace with growing demand. Crossing 400 fast chargers in the state is a reflection of that effort. It’s about giving riders the assurance that they’ll always find a charger when they need one. As we expand our retail presence, the charging network will continue to grow in tandem to make EV ownership truly seamless.”
eBikeGo Opens Acer Electric Vehicles Outlet In New Delhi
- By MT Bureau
- July 23, 2025
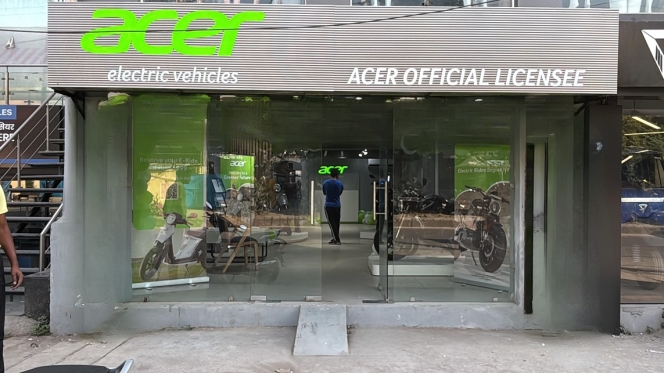
eBikeGo, an Acer Official Licensee and one of India’s electric mobility leader, has opened its first Acer Electric Vehicles retail outlet in New Delhi’s Okhla Industrial Area (Phase 2). This marks the beginning of a nationwide expansion, with 15 flagship stores planned to showcase Acer-branded e-vehicles.
The store offers a premium range of e-bicycles, e-scooters and e-bikes, blending global design with rugged Indian road adaptability. Targeting urban commuters and eco-friendly riders, the lineup includes e-cycles starting at an introductory price of INR 35,999, with e-scooters and e-bikes arriving soon.
Hari Kiran, Co-Founder & COO, eBikeGo, said, “We at eBikeGo are elated to announce our significant expansion in 15 cities across PAN-India, which has been made possible within only a few months, based on our strategic approach of setting up Acer Electric Vehicles retail outlets across various states. This rapid expansion underscores our commitment to eco-friendly transportation while positioning eBikeGo as a pivotal player in the Indian EV market and promoting a green and sustainable future for all Indians. It also enables us to put the spotlight on eBikeGo’s brand new e-2Ws products’ lineup, including our e-cycles, e-scooters and e-bikes.
“The overwhelming response we have received for eBikeGo’s store expansion and the feedback we have received for Acer brand serves as a testament to the strong brand appeal and speaks volumes about our credibility. With our wide portfolio of reliable EVs tuned to the Indian roads and consumer requirements yet boasting world-class standards, we shall continue to expand and grow our retail store network furthermore across the nation.”
Comments (0)
ADD COMMENT