NueGo Expands Inter-City Network with New Routes
- By MT Bureau
- October 22, 2024
Greencell Mobility brand, NueGo jas introduced six new intercity routes across the country in its efforts to promote sustainable mass mobility.
Currently operating in over 110 cities with 100 percent electric buses that are equipped with comfortable seats and subject to 25 rigorous safety checks, including mechanical and electrical inspections, the six new routes include Gurgaon–Dehradun, Noida–Dehradun, Noida–Chandigarh, Coimbatore–Madurai, Bangalore–Mysore and Bangalore–Vellore.
Touching on his company’s recent Kashmir to Kanyakumari expedition that highlighted the resilience of electric buses across diverse terrains, Devndra Chawla, CEO and MD, GreenCell Mobility, said, “We are announcing an extensive expansion of NueGo’s services across the country. This move aligns with our mission to improve intercity travel along with superior guest experience. With these new routes, we aim to enhance the connectivity for our guests while contributing to a greener future”
Launched in 2022, NueGo operates over 250 buses running over 450 departures daily.
- Switch Mobility
- Ashok Leyland
- Hinduja Group
- Mauritius
- Dr Navinchandra Ramgoolam
- Osman Mahomed
- Anurag Srivastava
- National Transport Corporation
- Convergence Energy Services
- RG Venkataraman
Switch Mobility Begins Exports Of Made-in-India E-Buses To Mauritius
- By MT Bureau
- August 08, 2025
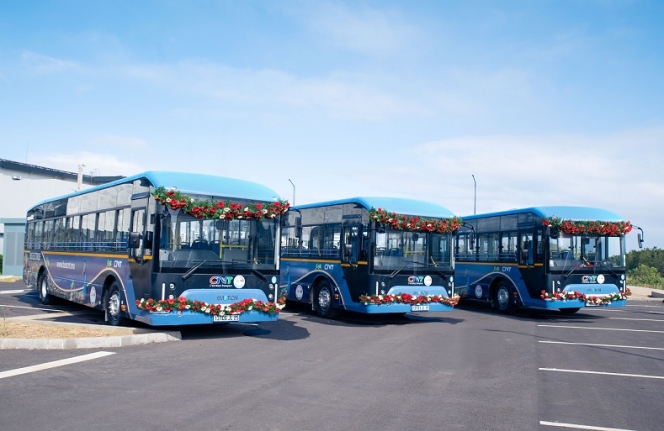
Switch Mobility, the e-buses and LCV business of the Hinduja Group, has flagged off the first batch of 10 electric buses (out of 100 e-buses) for the National Transport Corporation (NTC) of Mauritius.
The e-buses are said to be a special gift from the people and Government of India to the people and Government of Mauritius. The ceremonial launch was graced by Dr Navinchandra Ramgoolam, GCSK, FRCP, Prime Minister of the Republic of Mauritius; Osman Mahomed, Minister of Land Transport; Anurag Srivastava, High Commissioner of India to Mauritius and other eminent dignitaries from India and Mauritius.
The 100 Switch EiV12 buses are purpose-built, developed in Chennai and can seat up to 45 passengers. The buses are delivered through an open tender conducted by Convergence Energy Services (CESL) in India, will be operated by the National Transport Corporation (NTC), Mauritius' state-owned public transport operator.
RG Venkataraman, Chief Commercial Officer, Switch Mobility, said, "We are proud to deliver our Switch EiV 12 electric buses to Mauritius, a key milestone that brings our 'Make in India, for the World' vision to life. The Switch EiV12 buses, which integrate advanced global technology with the strength of Indian manufacturing, support Mauritius’ vision for a sustainable and healthier future. This partnership reflects our shared commitment to clean mobility, enhanced urban transport, environmental preservation, and improved quality of life for Mauritian citizens. Through our intelligent technology we are dedicated to empowering Mauritius with smart, efficient, and eco-friendly transportation solutions that will drive progress towards cleaner, more resilient cities."
The Switch EiV12 efficient rear-end dual-gun charging interface ensures rapid recharging and also optimises depot spaces. It is powered by Switch iON, the proprietary telematics system, that offers real-time vehicle health monitoring, ITMS, and efficient fleet management. The company shared to prioritise passenger safety, the bus is equipped with an advanced Fire Detection and Suppression System (FDSS). The floor-mounted LFP batteries contribute to a lower centre of gravity, ensuring excellent vehicle stability.
Ather Energy Launches Rizta E-Scooter In Nepal
- By MT Bureau
- August 07, 2025
Bengaluru-based electric two-wheeler maker Ather Energy has expanded its product line-up in Nepal with the introduction with the Ather Rizta e-scooter.
It was in November 2023 that Ather marked its entry in Nepal with the Ather 450 series and most recently introduced the 2025 Ather 450 in the region. Since then, it has established 9 Experience Centres and 6 Service Centres in the region along with 22 Ather Grid fast chargers.
Ravneet Singh Phokela, Chief Business Officer, Ather Energy, said, "Nepal was our first international market, and over the last two years, we have seen strong consumer interest and a very encouraging response to the Ather 450 series. To meet the growing demand, we have also steadily expanded our footprint across the country. With the launch of the Rizta, we are tapping into a new segment of family buyers who prioritise comfort and convenience in their everyday rides. We are hoping to see the same strong response for the Rizta as we’ve seen for the 450 series."
Polestar 4 Wins Red Dot Best Of The Best Award
- By MT Bureau
- August 06, 2025
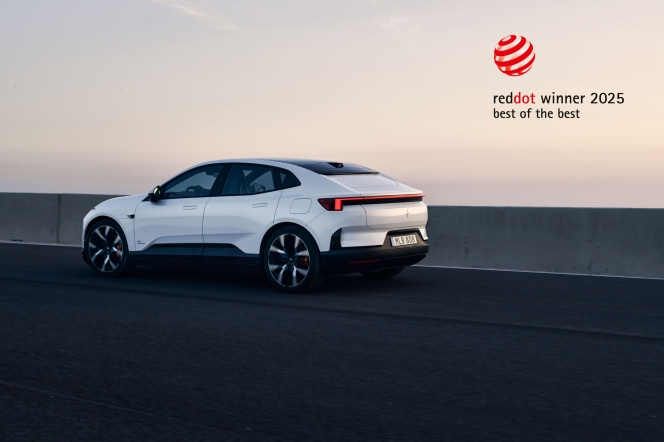
Swedish electric performance car brand Polestar has earned further acclaim for its innovative design philosophy. The Polestar 4 has secured the coveted Red Dot ‘Best of the Best’ award for 2025 in the Product Design category, celebrating its meticulous craftsmanship and bold design language. Both the Polestar 3 and Polestar 4 also received the Red Dot Label in the same category.
As one of the world's most prestigious design competitions, Red Dot acknowledged the Polestar 4's standout feature – its unconventional rear-windowless design – while praising its seamless fusion of coupe-like dynamism and SUV functionality. Additional design highlights include sleek frameless mirrors, distinctive dual-blade headlights and celestial-inspired ambient lighting, all contributing to its award-winning aesthetic. The ‘Best of the Best’ honour represents the highest Red Dot recognition, awarded only to groundbreaking designs that redefine industry benchmarks. An international jury of design experts rigorously assesses each entry through hands-on evaluation across multiple criteria.
This latest achievement builds on Polestar's strong Red Dot legacy, which includes prior "Best of the Best" wins for the Polestar 2, Brand of the Year distinction, and recognition for brand identity and design literature. These accolades reinforce Polestar's position as a leader in automotive design innovation.
“The Polestar 4 impressively succeeds in harmonising the technical complexity of such an advanced vehicle with design qualities such as simplicity and clarity,” remarked the jury.
Philipp Römers, Global Head of Design, Polestar, said, “This recognition is a testament to the dedication and passion of the Design Team here at Polestar. We are thrilled to see the work and commitment to distinctive design resonate with the jury.”
Exicom Raises INR 2.59 Billion Via Rights Issue
- By MT Bureau
- August 05, 2025
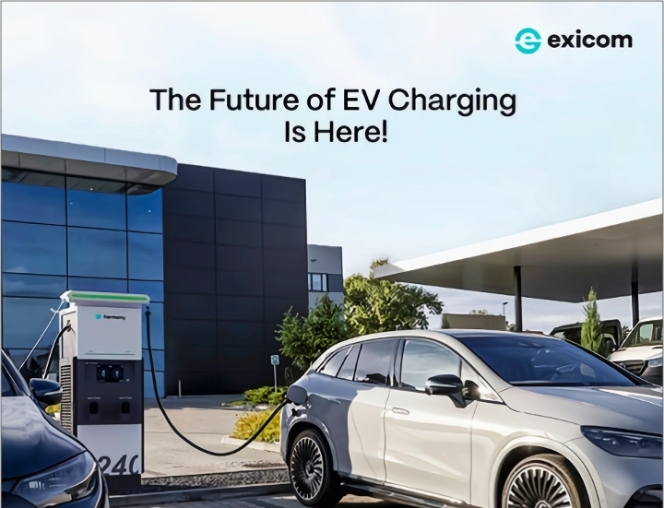
Exicom Tele-Systems Limited, a leading Indian manufacturer of EV charging and critical power solutions, has successfully raised around INR 2.59 billion through its recently concluded Rights Issue. The offering, which saw strong oversubscription, highlights sustained investor confidence and robust promoter support.
The Rights Issue, open from 15 to 30 July 2025, allotted 1,814,000 fully paid-up equity shares at INR 143 per share in a 3:20 ratio for eligible shareholders as of the record date 7 July 2025. Promoters demonstrated their commitment by subscribing to approximately INR 1.20 billion, reinforcing their belief in Exicom’s future growth.
Proceeds will primarily strengthen the company’s financial position by reducing debt, with a target debt-to-equity ratio of 1:4 by FY26. The funds will also support global expansion efforts, including enhancing market presence in the US, Europe and Australia through Tritium, alongside covering general corporate expenses. This successful capital raise positions Exicom to accelerate its EV charging and energy solutions business while driving long-term value for stakeholders.
Anant Nahata, Managing Director and CEO, Exicom, said, “We are grateful to our shareholders for their continued trust in Exicom. The capital raised will strengthen our balance sheet and support our expansion, particularly in international markets through Tritium. While Tritium’s turnaround is taking time, we are in advanced discussions for several large global high-power charger deals that we believe can help change the course of the company. We will see this fully play out starting FY27. Back home, we remain strongly optimistic about the India opportunity, driven by the steady growth in EV adoption across the country. Our Harmony Direct 2.0 continues to gain traction, with early momentum translating into a strong sales pipeline. Meanwhile, Spin Air home chargers are securing consistent wins with leading OEMs, reinforcing trust in our technology and execution."
Shiraz Khanna, Chief Financial Officer, Exicom, said, "This Rights Issue marks an important step in enhancing our financial health. The capital raised will enable us to significantly reduce debt and support sustainable growth while maintaining prudent capital discipline."
Comments (0)
ADD COMMENT