Narrower, Bigger Diameter Tyres Of EVs Encourage Innovation Around Them
- By Bhushan Mhapralkar
- January 14, 2025
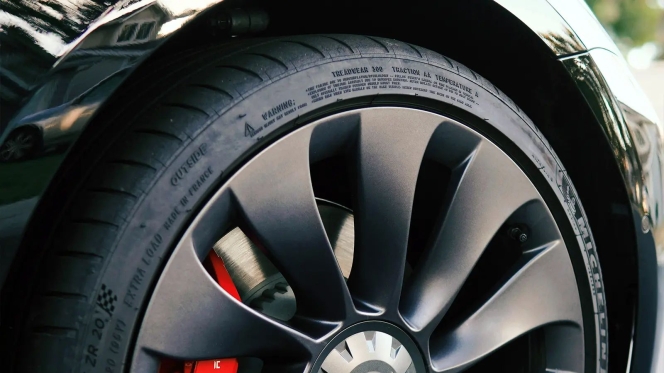
The narrower, bigger diameter tyres of electric vehicles are encouraging innovation around them. Supporting lower rolling resistance, the tyres are pushing suppliers and OEMs to explore new technological innovations. A leading German auto supplier for example has developed a ‘mechanical’ technology to ensure superior manoeuvring with near 180 degrees turn of the steered wheels.
This is a development that could be applied to ICE rear-wheel drive vehicles as well. Even, light-duty commercial vehicles such as the Tata Ace/1000 or the Switch Iev3/Iev4 that are aimed at the last mile delivery segment were backing up into a tight parking spot or navigating through a narrow lane is part of the job.
As designers and engineers toy with the idea of larger wheel wells and the ability of the steered – front – wheels to turn as much as 180 degrees, the use of narrower, bigger diameter tyres with low rolling resistance in electric vehicles is spurring yet another round of innovation, albeit as a part of the entire platform architecture that is rather software driven and subject to much virtual development in the interest of ‘time-to-market’ and a differentiated user experience.
With over 14 million small electric vehicles sold in 2023 the world over, the push has been to develop tyres that enhance operation and performance. Provide a typical ‘family’ car the ability to transform into a sports car given the wave of high torque available from the word ‘go’ in an electric vehicle.
With electric vehicle sales poised to increase 17.5 percent year-on-year globally to bridge 41.2 million units in 2029, electric vehicle tyres are expected to facilitate a further drop in rolling resistance while employing sustainable raw materials, technologies and manufacturing processes.
A sustainable EV tire design should consider the whole lifecycle of the product. Tires can be composed of well over 100 different raw materials. These are mixed and the rubber compounds are machined resulting is several components of the tire construction. EV tires are expected to be stronger and lighter, with less rolling resistance due to its importance in CO2 emissions and fuel consumption.
A key challenge being the development of tyre formulations for electric vehicles with the tread compound that is more resistant to abrasion, it is the instant torque availability that is necessitating tyres that may look like ICE vehicle tyres but are quite different in the way they handle traction and aid a longer drive range. There is the issue of kerb weight as well, not to overlook the new environmental pressures for durability and abrasion resistance.
Interestingly, new opportunities are being created on the vehicle engineering and dynamics side as well as on the side of electric vehicle tyre development and manufacture.
Starting with materials that are broadly classified as ‘renewable’ (can be sustained on time) and as ‘recycled’ (re-used and made from recovered end-of-life tyres), it is the tandem mixers that are producing more homogeneous rubber compounds, including tread compounds that employ optimised silica fillers.
Tyres for electric vehicles are demanding the use of triple or quadruple extruders for treads and sidewalls as per the vehicle weight, application and dynamics. Roller head or roller die units are also being used to produce inner liners as a single or multilayer sheet
In terms of textile coating of steel cord components in e-vehicle tyres, four-roll and Z-type calendars are used. Also, full tyre assembly machines that can produce tyres to tighter tolerances, higher specs such as superior uniformity and sans operator invention.
With electric vehicle tyres and ICE vehicle tyres being tested and validated differently primarily because of the higher load bearing capacity and low rolling resistance, electric vehicle tyres are made up of a different (softer) rubber compound than regular tyres with an eye on less noise, mentioned a testing expert at an OEM that is increasingly producing electric vehicles in India.
Pointing at an electric passenger vehicle the company launched in India recently, he averred, “Softer compounds are used to ensure less rolling noise and better transmission of torque from the motors to the road.”
With finer tolerances in need, optical machine vision systems for end-of-line quality inspections, including new technologies such as X-rays to check steel belts, cords and bead reinforcement are increasingly used.
They are used to check for air bubbles in inner liners as well. Advances in tyre design and manufacture include new developments in simulation software to model the performance of new designs quickly. This is without material input cots.
AI is being increasingly used to ensure superior analysis. AI is also used to automate manufacturing process as part of Industry 4.0 workflows.
Mercedes-Benz Marks 600,000th G-Class With Electric Model
- By MT Bureau
- August 06, 2025

German luxury carmaker Mercedes-Benz has attained another milestone by rolling out the 600,000th Mercedes-Benz G-Class from Graz, Austria. The milestone vehicle is an electric G 580 with EQ Technology finished in obsidian black metallic.
Since its launch in 1979, the G-Class has become a symbol of off-road capability and design. The first G-Models combined off-road performance with on-road comfort and Mercedes' safety standards. In the past four decades, it has evolved while retaining key features such as all-wheel drive, differential locks, and a ladder frame. Design elements like the round headlights and exposed spare wheel remain.
In celebration of its heritage, a limited edition, the G-Class Edition Stronger Than The 1980s, was released last year. This model paid homage to the original W 460 series.
The brand's customisation service, Manufaktur, has seen increasing popularity. Since 2019, over 90 percent of G-Class customers choose at least one Manufaktur option, averaging three per vehicle. Customers can now select from up to 20,000 paint colours, including heritage shades.
VinFast Inaugurates Tamil Nadu EV Plant
- By MT Bureau
- August 04, 2025
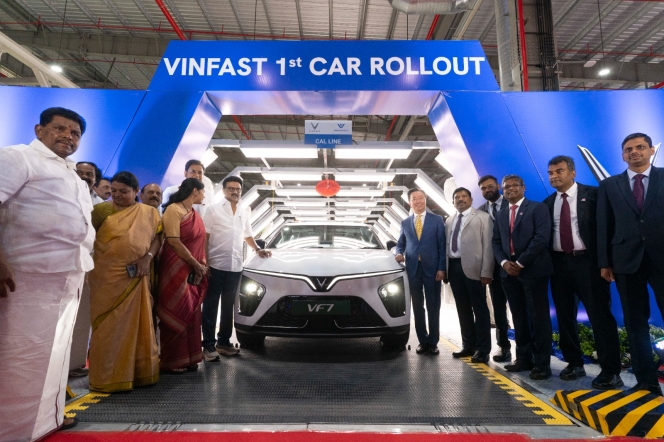
Vietnamese automaker VinFast has officially inaugurated its electric vehicle assembly plant at SIPCOT Industrial Park in Thoothukudi, Tamil Nadu, India.
The new facility is VinFast’s third operational plant and the fifth project in its global manufacturing network. It is part of the company’s long-term bet on selling its vehicle in the world’s third-largest automobile market.
The factory is spread across 400 acres and is equipped with state-of-the-art production lines, featuring advanced automation and technologies. The complex houses multiple workshops, including body shop, paint shop, assembly shop, quality control centre, and a logistics hub. It also includes an auxiliary cluster for local contractors, which is expected to expand in the coming years.
The company expects to create around 3,500 jobs for local workers at full capacity, along with several thousand indirect jobs in the supply chain ecosystem. To start with, the company will assembly the VF 7 and VF 6 electric vehicles with a capacity of 50,000 units per annum, which can be scaled upto 150,000 units per annum to meet market demand.
VinFast states with the Tamil Nadu plant on stream, it moves closer to its 2025 sales target of 200,000 vehicles and its long-term production goal of 1 million vehicles per year by 2030.
Pham Sanh Chau, CEO, VinFast Asia, said, “The VinFast Tamil Nadu plant marks a strategic milestone in our long-term commitment to the Indian market. It establishes a strong foundation for sustainable growth and positions us to offer high-quality, competitively priced electric vehicles to Indian consumers. Looking ahead, the facility will expand its production capacity to meet rising demand. We aim to develop it into VinFast’s largest export hub for South Asia, the Middle East, and Africa. In fact, we've already secured initial orders from several countries across these regions. In close collaboration with the Tamil Nadu government, VinFast is working to transform the area into the 'EV capital of South Asia'—supporting both the dynamic domestic market and our broader regional ambitions.”
Going forward, VinFast aims to further promote localisation, technology transfer and also upskill its workforce.
China’s NIO Surpasses 800,000 Vehicle Production Milestone
- By MT Bureau
- July 28, 2025
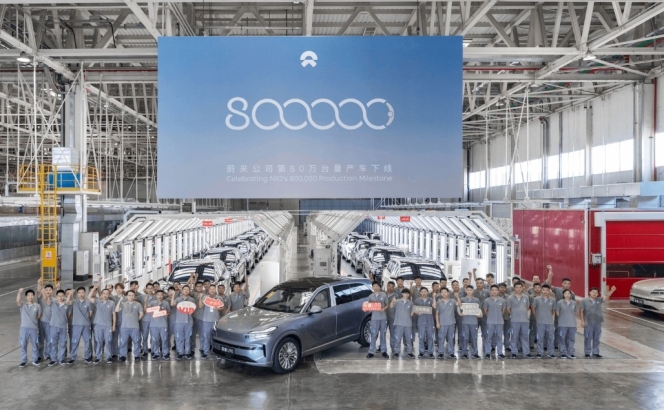
Chinese electric vehicle manufacturer NIO has attained a new production milestone with the 800,000th unit – Onvo L90 – rolling out from its Factory One in Hefei on 24 July 2025.
Since the pre-order started on 10 July, the company shared that the L90 has received widespread interest and recognition from users and the market.
Built on NIO’s decade of investment in the charging and swapping infrastructure, the L90 redefines the family-oriented three-row electric SUV by tackling two major user pain points: charging anxiety and space anxiety.
The test drives for the L90 officially began on 23 July with nearly 600 test drive cars now available at over 400 ONVO stores and showrooms in 140 cities in China. The L90 is set to be officially launched on 31 July, with deliveries starting 1 August.
- Association of Indian Forging Industry
- AIFI
- Bureau of Energy Efficiency
- BEE
- Assistance for Deployment of Energy Efficient Technologies in Industrial Establishments
- ADEETIE
- Yash Munot
- Deven Doshi
- Manohar Lal
AIFI and BEE Sign MoU to Advance Energy Efficiency in Forging Sector
- By MT Bureau
- July 21, 2025
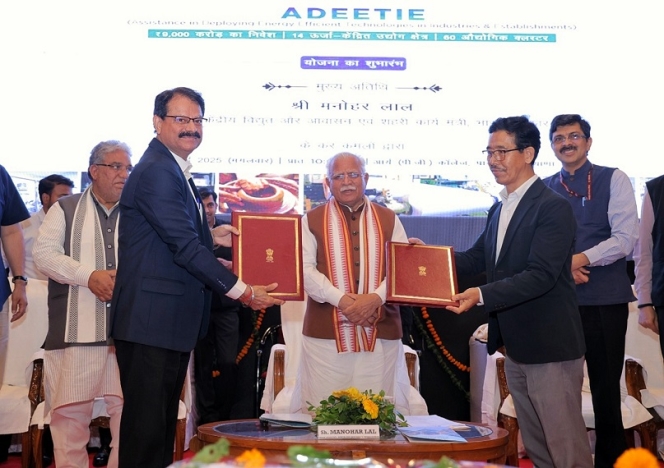
The Association of Indian Forging Industry (AIFI), the apex representative body of the Indian forging sector, has signed a Memorandum of Understanding (MoU) with the Bureau of Energy Efficiency (BEE), Ministry of Power, Government of India.
The agreement was signed in the presence of the Union Minister of Power and Housing & Urban Affairs, Manohar Lal, signifying an important step towards embedding sustainable manufacturing practices within the forging sector. It forms part of the newly launched Assistance for Deployment of Energy Efficient Technologies in Industrial Establishments (ADEETIE) scheme.
The ADEETIE initiative, announced by the Ministry of Power and managed by BEE, is focused on enabling micro, small and medium enterprises (MSMEs) across 14 energy-intensive sectors – including forging – to adopt advanced energy-efficient technologies. The scheme adopts a comprehensive approach, offering:
- Interest subvention on loans for technology adoption (5 percent for micro and small enterprises, 3 percent for medium enterprises).
- End-to-end support, including investment-grade energy audits, guidance with project execution and robust post-deployment monitoring.
- Establishment of a dedicated project management unit and a nodal banking partner to streamline the process.
With a total budget of INR 10 billion, the scheme aims to unlock more than INR 90 billion in overall investments, including INR 67.5 billion specifically set aside for MSME lending. This allocation is expected to reduce the financial burden for forging units seeking to embrace energy-efficient solutions.
Yash Munot, President, AIFI, said, “This collaboration with the Bureau of Energy Efficiency marks a significant step forward for the Indian forging industry. As one of the most energy-intensive sectors, forging stands to benefit immensely from the structured support offered under the ADEETIE scheme. By enabling access to financial incentives and technical guidance, this initiative will empower MSMEs to adopt cutting-edge, energy-efficient technologies. It aligns perfectly with our vision of building a globally competitive, environmentally responsible and innovation-driven forging ecosystem. AIFI is committed to mobilising our members across clusters to take full advantage of this opportunity and contribute meaningfully to India’s broader sustainability and industrial growth goals”.
Deven Doshi, Chairman – Government Interface, AIFI, added, “Energy efficiency is very essential for forging companies, but the MSME sector often faces structural barriers in adopting cleaner and more efficient technologies. The ADEETIE scheme provides a structured framework of support, including technical, operational and financial aspects, that directly addresses these challenges. AIFI is proud to be a partner in this transformative journey. This collaboration not only ensures sectoral compliance with energy norms but also paves the way for long-term industrial modernisation.”
The Indian forging industry, particularly its MSME segment, has been a foundation for the country’s manufacturing and export sectors, supporting diverse areas such as automotive, defence and capital goods. Despite this, the sector has historically faced high energy costs and sustainability challenges. The ADEETIE scheme is set to address these issues directly, equipping forging enterprises with fiscal support and technical know-how to achieve sustainable growth.
Through this MoU, AIFI will actively promote and facilitate the implementation of the ADEETIE scheme across forging clusters nationwide, ensuring that members gain timely access to tools, knowledge, and incentives needed to strengthen both competitiveness and environmental responsibility.
Comments (0)
ADD COMMENT